 |
This task explains how to create fillet surfaces between sets of surfaces and curves used as support
elements. |
 |
The fillet surface edges on the supports are defined by the radius or by support curves.
With additional radius parameters and options you can create a variety of surfaces.
The continuity between fillet surface and supports can be from G0 to G3.
The support surfaces can be trimmed.
As input elements and parameters must be specified at least two surfaces and one radius. |
 |
Open the AdvancedFillet.CATPart document. |
 |
-
Click the Advanced Fillet icon .
The Advanced Fillet dialog opens.
|
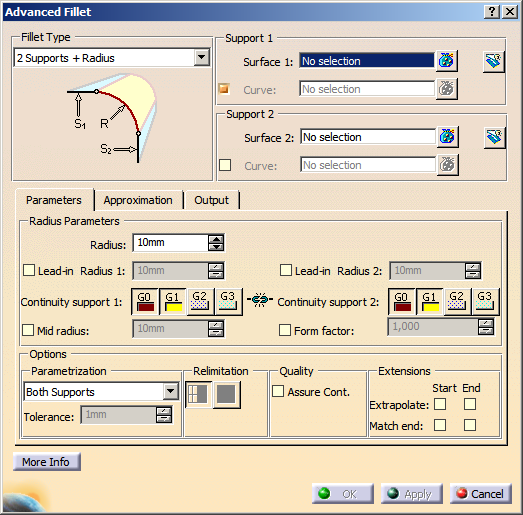 |
|
-
Select the fillet type 2 Supports + Radius.
-
Select Surface.1 and Surface.2.
|
|
-
Specify a Radius of 30 mm and click Apply.
A fillet surface with the specified radius is created at the two surfaces.
|
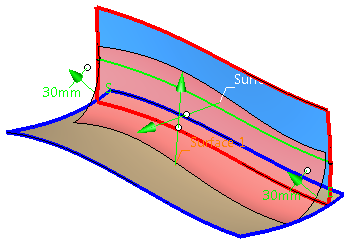 |
|
-
Modify the radius using one of the manipulators and the surface ends.
|
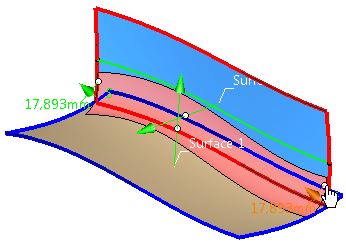 |
|
-
Change to fillet type 2 Supports + 1 Support Curve.
-
Activate the check box Curve in the Support 1 field and select Isoparameter.2 as support curve.
|
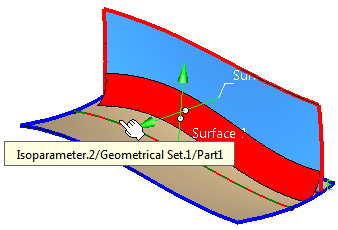 |
|
-
Click Apply to create a fillet surface using the selected support curve as fillet surface edge.
|
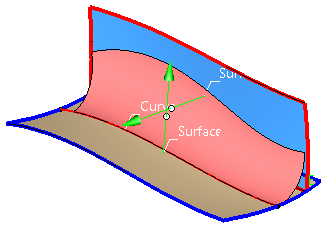 |
 |
You can define the following options:
Fillet Type: Defines which criteria to choose as input for the fillet creation.
In the Radius Parameters field the display and availability of the options changes according to
the selected fillet type.
The following fillet types are available: |
|
- 2 Supports + Radius
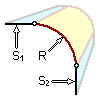
Defines the fillet surface by two supports and the Radius.
|
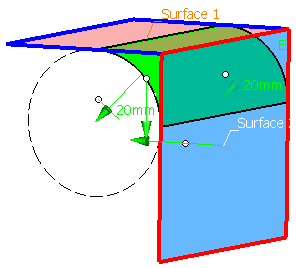 |
|
- 2 Supports + Chord Length
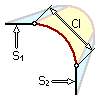
Defines the fillet surface by two supports and the chord length.
The chord length is the distance between both edges of the fillet surface lying on the supports.
|
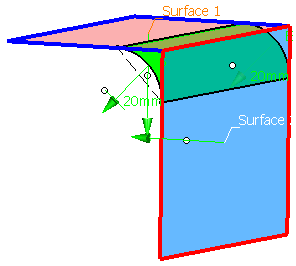 |
|
- 2 Supports + 1 Support Curve
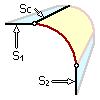
Defines the fillet surface by two supports and a support curve to be selected either on Support 1 or Support 2 with one of
the Curve options. The selected support curve is used as fillet surface edge.
The radius value derives from the support curve.
|
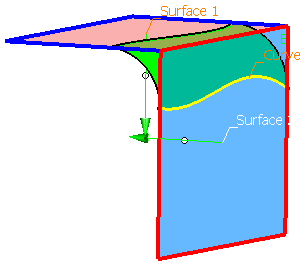 |
|
- 2 Supports + 3 Radii
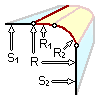
Defines the fillet surface by two supports, the Radius as well as two Lead-in radii (Lead-in Radius 1/2).
Depending on the selected radii you can create an asymmetric fillet surface.
 |
Note: To be able to create a fillet surface with three different radii, the Radius value must
lie between the values of Radius 1 and Radius 2, i. e. either Radius 1 must be larger
and Radius 2 smaller than Radius, or vice versa. |
|
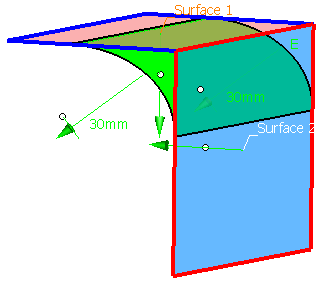
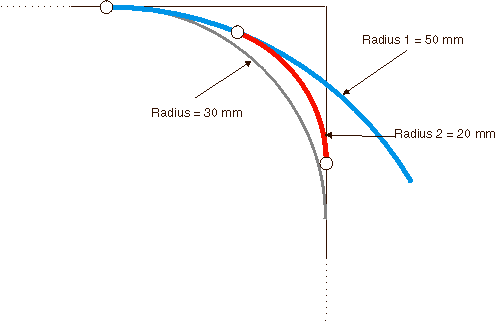 |
|
- 2 Supports + 2 Chord Lengths
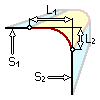
Defines the fillet surface by two supports and two chord lengths.
The chord length is the distance between the theoretical intersection point of the arc tangents and the fillet surface edge
on the corresponding support.
|
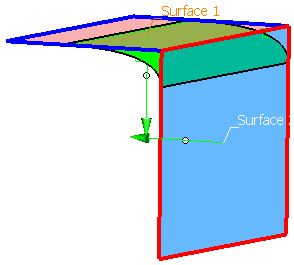
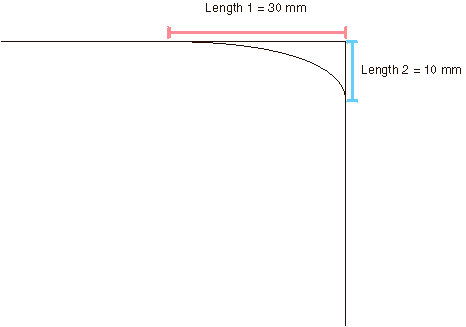 |
|
- 2 Supports + True Minimum Radius
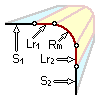
Defines the fillet surface by two supports and the true minimum radius.
Using the true minimum radius guarantees that the radius in the fillet curve will not fall below the specified value while
keeping the continuity set.
|
2 Supports + True Minimum Radius
with G1 continuity |
2 Supports + True Minimum Radius
with G2 continuity |
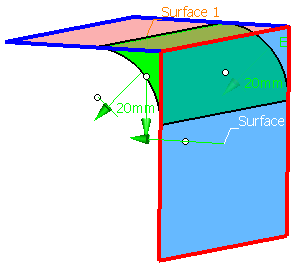 |
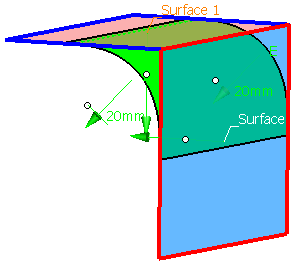 |
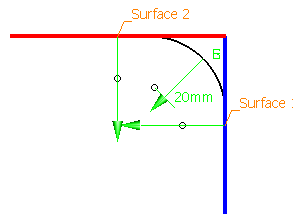 |
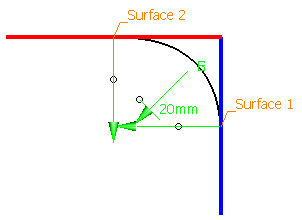 |
|
|
- Support 1 and 2 - Surface 1/2: Selects surfaces as supports.
If two or more support surfaces are selected, the normal direction of the first selected support surface is used.
Trim Support 1/2: Trims the support surfaces at the corresponding edges of the fillet surface.
- Support 1 and 2 - Curve: This option is only available for
2 Supports + 1 SupportCurve.
Support curves can be selected either on Support 1 or Support 2. The following element types can be selected:
Elements |
Sub Elements |
Type |
Curve |
3D Curve
Line
Offset Curve (Feature)
Project Curve (Feature)
Styling Corner (Feature)
Blend Curve (Feature)
Split Curve (Feature) |
Bezier, NURBS,
B-Splines, Join,
Surface Edge, Line,
Pline, Nupbscurve,
Spline, Conic |
If one of the check boxes for the curve selection is selected, Radius is disabled.
|
|
Parameter tab |
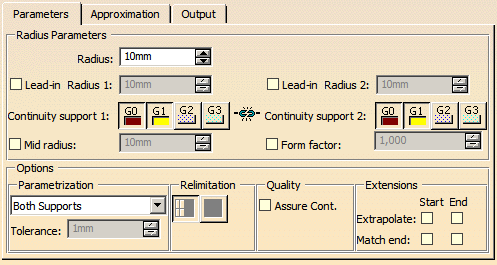 |
|
- Radius Parameters: The radius parameters to be defined depend on the fillet type
selected:
Fillet Type |
Radius Parameters |
Lead In Radius Parameters |
2 Supports + Radius |
Radius:
Definition of the fillet radius between two supports. |
Lead-in radius 1+2:
The lead-in radius defines an arc with tangent (G1) or curvature (G2) continuous transition to the support. The radius
value defines the point at which the lead-in radius starts. |
2 Supports + Chord Length |
Chord length:
Definition of the chord length. |
Lead-in radius 1+2 |
2 Supports + 1 Support Curve |
- |
- |
2 Supports + 3 Radii |
Radius
Definition of the first radius. |
Radius 1+2:
Definition of the second and third radius. |
2 Supports + 2 Chord Lengths |
- |
Length 1+2:
Definition of the chord lengths. |
2 Supports + True Minimum Radius |
True minimum radius:
Definition of the true minimum radius. |
Lead-in radius 1+2 |
- Continuity support 1/2: As transition quality between fillet surface and supports you can select for each side
a continuity from G0 to G3.
The minimum order of the fillet surface in arc direction depends on the selected continuity. The order can be increased via
the Approximation tab.
- Mid radius: Only available if Form factor is cleared.
For the middle of the arc can be defined a mid radius different from the radius.
The continuity is kept when the mid radius is modified.
The mid radius is applied along the center line of the radius value.
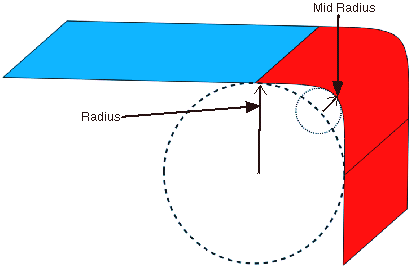
- Form factor: Only available if Mid radius is cleared.
Determines whether the fillet shall be more flat or more copped. The continuity to the supports remains unchanged.
Values smaller than 1 create flat fillets, values higher than 1 steep fillets.
Form Factor cleared |
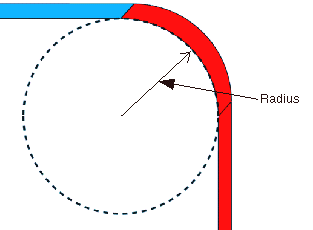 |
Form Factor 0.5 |
Form Factor 2.0 |
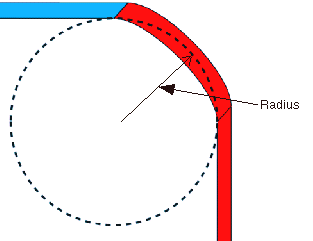 |
 |
- Options:
- Parametrization: Specifies how the parametrization of the fillet surfaces is influenced. The following options
are available:
- Support 1 / Support 2: Takes the parametrization from the 1st or 2nd set of support
surfaces, i. e. the segment boundaries of the support surface 1 or 2 determine the segment boundary of the created
fillet.
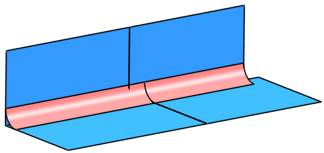
- Both Supports: Takes the parametrization from both sets of support surfaces.
At each segment boundary of the support surface clusters a segment boundary is inserted in the fillet surface. In
this case, very small segments may eventually be created.

- Stitch: If the distance between two segment boundaries of the support surfaces is smaller than the
Tolerance specified in the text box, only one segment boundary either from surface 1 or from surface 2
is taken.
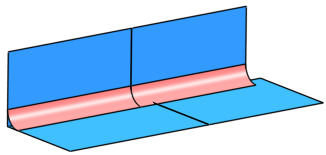
- Average: If the distance between two segment boundaries of the support surfaces is smaller than the
Tolerance specified in the text box, only one segment boundary is inserted in the middle between
the segment boundaries of the support surfaces.
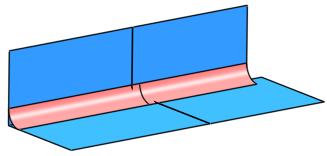
- Tolerance: Only available for the parametrization options Stitch and Average.
The initial segmentation of the fillet is increased until the tolerance is kept, i. e. if the distance between two segment
boundaries of the support surfaces is smaller than the tolerance, instead of two segment boundaries only one boundary
is inserted depending on the selected parametrization.
- Relimitation: Only available if Extrapolate and Match End are selected.
The fillet surface can be trimmed as a face or trimmed and reapproximated as surface (no face).
Trim
Face: The basic surface remains unchanged.
Trim
Approx:The basic surface changes. The result is not a face.
- Assure cont.: In the resulting geometry the specified continuities should be respected within the tolerances
specified on the Topology tab in Tools > Options > Shape > ICEM
Shape Design.
In configurations not allowing the compliance of all continuities – especially for G2 fillet surfaces, this option keeps
the continuity at the different transition types with following priority:
1. transition A : transition between fillet ribbon and support surfaces within the specified tolerance, then
2. transition B : transition between elements of the fillet ribbon within the specified tolerance, then
3. transition C : transition on fillet traces within the specified tolerance.
Exception: G1 continuity is very important for the transition types A and B. So if it is not possible to have G2
for transition type A and G1 for transition type B, G1 will have priority for both transition types A and B.
- Extensions:
- Extrapolate: If the connecting edges of the support surfaces have different lengths, the fillet surface
can be extended to the exterior edges of the support surface with the larger extent. The extrapolation can be activated
for the start and/or end edge curves of the fillet.
Extrapolate cleared |
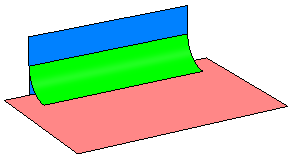 |
Extrapolate Start selected |
Extrapolate Start and End selected |
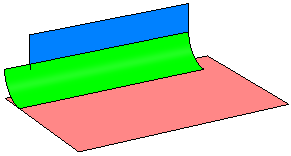 |
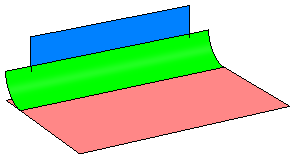 |
- Match end: The start and/or end curve of an extrapolated fillet surface (Extrapolate selected)
can be matched to the exterior edges of the support surfaces creating a tangent continuous transition.
Match end Start selected |
Match end Start and End selected |
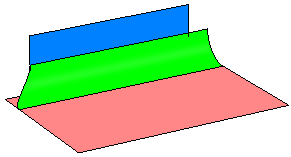 |
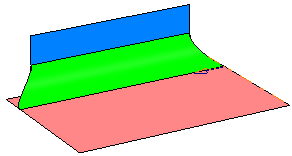 |
Match end Start and End selected
with trimmed support surfaces |
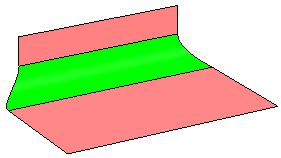 |
|
|
See Approximation tab |
|
See Output tab |
|
Click 'More Info' to display deviations and output results. |
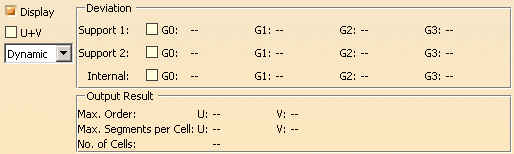 |
|
- Display: Depending on the options selected, values are displayed in the graphics area.
- Deviation:
- Support 1/2: Indicates the maximum deviation of the fillet surface from the support surfaces.
- Internal: Indicates the maximum internal G1, G2, and G3 deviation between the different created fillet surfaces.
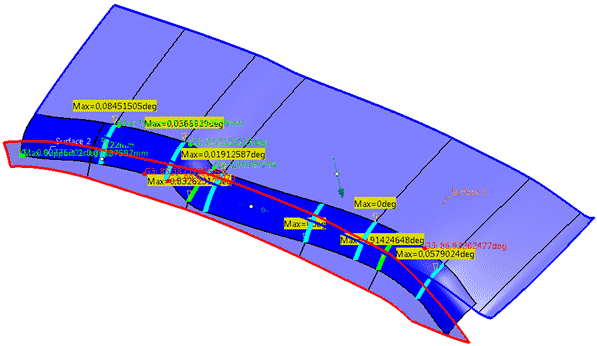
- Dynamic, Static, None: See Apply Modes
- U+V: Display of the UV vectors of the created fillet, and, if Trim Support is activated,
its support.
- Output Result: See Output Result
|

|