 |
This task shows you how to
extract geometrical or electrical bundles with all the devices that are
associated to them, such as their connectors, back shells, shells, contacts
and supports from a 3D model. |
 |
Open the
ElectricalAssembly.CATProduct document.
Keep open the Flattening Assembly document you have created in the
previous task.
If you have forgotten to open a second
document, a warning message will be displayed. |
 |
-
Select
Windows > Tile Horizontally to get a better viewing of the
process.
-
Click Extract
.
|
When duplicating an electrical bundle,
all the links with the geometrical bundles associated to it are
maintained.
|
-
Select an electrical or
geometrical bundle in the geometry area or in the specification tree.
 |
-
Selecting the Electrical
connection check box in
Tools > Options
> Equipment & Systems >
Electrical Harness Flattening >
General
tab allows the system to automatically check the electrical
connections. For more information refer to
Electrical Harness Flattening.
-
By default,
the system checks the electrical connections. In the 3D harness, at
the same geometrical location if two bundle segment extremities are
not connected, an error is displayed:
The network checker has detected some errors
on the 3D Harness electrical connections. Do you want to correct the
electrical links?
-
If you
click OK, the network checker creates the electrical
link between the bundle segment extremities. You need to save
the modification.
-
If
you click Cancel, the extraction process stops.
|
The result looks like this. |
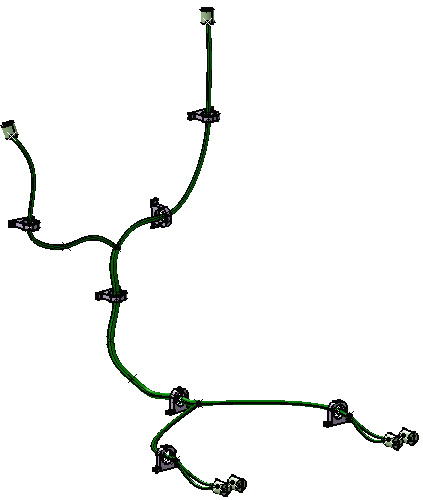 |
-
Save your data.
Notes:
|
|
-
The build mode of
bundle segments is maintained after extraction.
-
The
build mode of bundle segments, except for those
based on mechanical splines (see below) will be automatically set
to
Length
Mode after flattening,
so that the flattening process does not modify bundle segment
lengths.
If bundle segments are built in Slack Mode, a minimum
slack of 0.1% is recommended. If zero slack is used, this may
generate update errors when extracting 3D data.
Bundle segments based on mechanical splines and built in Slack
Mode will be extracted in Slack Mode. This may
have repercussions when flattening, straightening and manipulating
these segments.
-
You can also extract bundle segments created along
external curves.
-
The knowledge parameters on the bundle
segments are copied to the extracted harness when
extracting 3D data.
 |
- Ensure that the knowledge parameters are added
to the bundle segment using the
Tools >
Formula..
command in the
original document to maintain all the parameters
during extract. For more information,
refer to
Knowledge Advisor User's Guide: Creating
a Parameter.
- The knowledge parameters added to the bundle
segment using the Parameters Explorer command
in the Knowledge Advisor workbench are also
maintained during the extraction of data. For more
information,
refer to Knowledge Advisor User's Guide: Adding a Parameter to a Feature.
|
-
A link is created between the 3D harness and the
extracted view. It can be browsed using the Edit > Links
command.
-
Mechanical parts
located in geometrical bundles are extracted as instances.
To handle mechanical parts correctly, publish any points serving to
route the bundle segment along the part and give these points a
unique publication name. Use published points when routing bundle
segments.
-
A green line is
created during the Extract process between the bundle segment
and the published point of a support.
-
During the extraction process of a backshell
supported by support, only the attributes of support are
extracted
and synchronized.
|
|
 |
- While using the Extract command on documents
created in V5R11, an error message may appear saying: An error has occurred
during the data duplication.
You can try to use the CATDUA utility to clean the data and
recover the correct geometry. Refer to
Using the Data Upward Assistant.
- Ensure that only one document corresponding to 3D Install
Harness assembly (products and parts) is opened in the editor at
the time of performing the extract. Else, there will be some
errors during the extract process which may lead to corrupt
data. However, if the user happens to commit this mistake, i.e.
open 2 windows in 3D design data, an error message appears
saying: An error has occurred during the data duplication.
However, please note that this error box can come for other
reasons also.
|
|
About Extract Command
The command enables to extract the connected network from the first
identified object in your selection. For example, it can be:
- The first multi-branchable under a geometrical bundle
- The first branchable under an multi-branchable
- The first geometrical bundle under an electrical bundle
|
 |
- This behavior is not applied for geometrical
bundles
that are not part of a selected electrical bundle
or
selected electrical geometries. The geometrical bundles that are
not selected are not extracted even if they are connected to the
network.
- A geometrical bundle below another geometrical bundle is
not extracted if the parent is selected for extract. When a
multi-branchable is selected for extract, all the geometries
connected to the same network are extracted.
|
|
|
Extracting 3D Data using the Synchronize Algorithm
To use the Synchronize algorithm in order to ensure better PLM
integration and obtain a HTML report on the Extract process, select the
Synchronize option (Tools > Options > Equipment & Systems >
Electrical Harness Discipline > Electrical Harness Flattening > General). |