 |
This task shows you how to create iso-thickness areas (ITA) to make
the design quicker and easier.
Read About Iso-Thickness Areas for
more information, in particular about limits and possible problems. |
 |
Open the GridJunctionLines01.CATPart
document. |
 |
-
Click Iso-Thickness
Areas
in the Top Surface & Solid toolbar. The
Iso-thickness Areas dialog box is displayed:
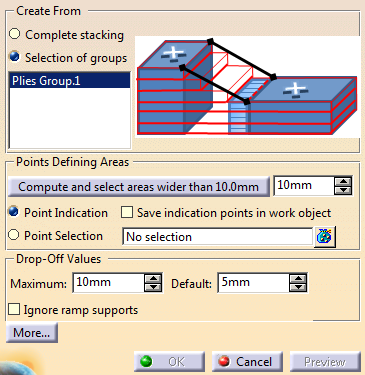
The plies groups found in the model are displayed in the dialog box.
-
Choose a Create From option:
- Complete
stacking: The
complete stacking is
selected,
the plies
groups listed in the
dialog box are no longer
selectable.
-
Selection of
groups: Select the
required groups from the
list in the dialog box.
Multi-selection is
possible.
|
Select core sampling points to define the iso-thickness
areas manually:
- Either select the
Point Selection option,
and select exisiting
points in the 3D viewer.
- Or select the
Point Indication option
and pick locations in
the 3D viewer.
- Then decide if you
want to save those
indication points in the
in work object or not.
- If required, create
additional points using
the contextual menu.
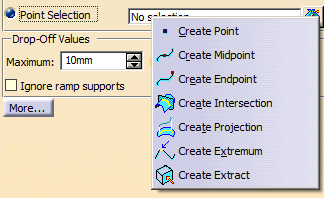
- You can mix both
options, e.g. select
existing points, then
indicate points to
complete the selection.
- Multi-selection is
available through
and the dialog box
below:
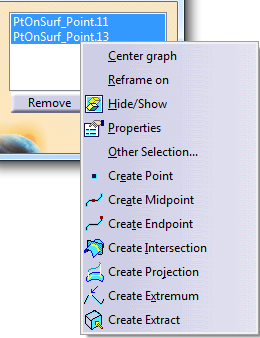
- The number of points
selected or indicated is
displayed in the dialog
box.
|
-
To define the iso-thickness areas automatically:
- Enter a value in the
spinner under Points
Defining Areas.
This value represents
the minimum width that
makes an iso-thickness
area selectable.
By default, this value
is set to the maximum
drop-off value.
It varies with the
maximum drop-off value.
You can also edit it
manually.
- Click Compute and
select areas wider than
...
- This
button
is
available
only
once in
creation
mode.
- This
button
is not
available
in
edition
mode.
We recommend that you consider this
automatic mode as an initialization
step,
to be completed manually.
- Potential iso-thickness
areas are computed.
- Those wider than the
value entered are
automatically selected.
- A progress bar is
displayed.
- Indication points
are created and selected
as you would have done
manually.
|
-
For models not designed with a grid approach,
define the
Drop-Off Values used to compute the bottom of slope.
By default:
- Maximum is set to 0
if no ramp support has
been defined,
or to the
maximum step of slope
found in all ramp
supports of the model
otherwise.
- Default is set to 0
if no ramp support has
been defined,
or to the
minimum step of slope
found in all ramp
supports of the model
otherwise.
|
|
|
Optional: Select the Ignore
ramp supports check box. This is useful when ramp supports do
not fully fit your requirements.
(The first curve in the ramp support is not the top one, or you need to
extend plies by a symmetry). This options applies to the
iso-thickness areas group, not to individual iso-thickness areas.
When this check box is selected, the shells are relimited by the bottom
slope, computed with the distance to neighboring ply contours, with a
geometrical approach. If this automatic computation fails, you can
relimit specific shells using standard relimitation commands. |
|
-
Click More...
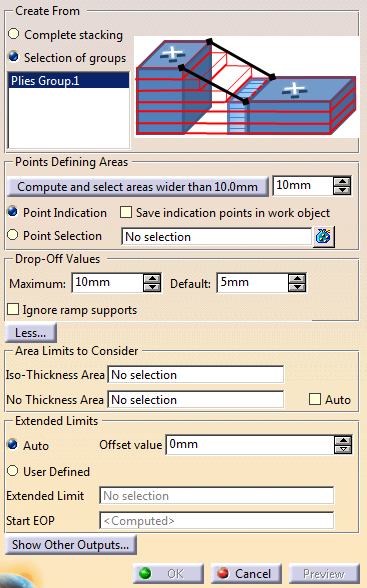
-
Select a contour or Composites geometry and the
required method to create limits.
-
Iso-Thickness Area: Creates the ITA group only inside the
selected area (one selection permitted).
The top surface
generated from this ITA group is limited by the contour or
geometry.
- No Thickness Area: Creates the ITA group with
all the areas found inside the selected contour or geometry,
even it the areas have no plies, thus no thickness with
respect to the support surface.
The top surface generated from
this ITA group contains these areas with no thickness.
- Make
sure the
Not Thickness Area does not intersect a
ply contour.
|
-
Extend the limits of the ITA Area:
-
User Define: Select an
Extended limit (Contour or Composites geometry), and an optional
Start EOP (Contour or Composites geometry) to specify the side of the ITA to extend.
- If you do not select a
Start EOP, it is computed as the full ply boundary of all selected plies groups.
-
Start EOP and
Extended limit
must be larger than all selected plies.
- Auto: Enter an offset value (Extended limit and
Start EOP are automatically computed).
- The offset value cannot result in a top surface larger than the support surface.
-
Auto does not support multi-domains EOP.
|
-
Click Show Other Outputs:
-
Select the Generate
shell boundaries
checkbox to compute
shell boundaries
automatically
for each iso-thickness area
shell.
By default, Generate
shell boundaries is not
selected.
-
Select the Generate
offset surface checkbox
to compute an offset
surface automatically
for each iso-thickness
area shell.
By default, Generate
offset surface is not
selected. It is
available only in
creation mode.
|
Under Modifiers, define an additional thickness.
- It is entered as a
ratio of the current
thickness, e.g. 0.1
means 10% of the current
thickness.
- In creation mode, it
defines the additional
thickness of all the iso-thickness
areas of the group.
- In edition mode:
- If
an
additional
thickness
previously
applied
to all
the iso-thickness
areas of
the
group,
the
modified
additional
thickness
applies
to all
the iso-thickness
areas of
the
group.
- If
an
additional
thickness
applied
only to
some iso-thickness
areas of
the
group,
you can
choose
to apply
the
modification
only to
those iso-thickness
areas or
to all iso-thickness
areas of
the
group.
- By default,
Additional thickness
ratio is set to 0.
|
-
Click Preview to check any changes.
The edges of the iso-thickness areas that correspond to the bottom
slopes are highlighted in green.
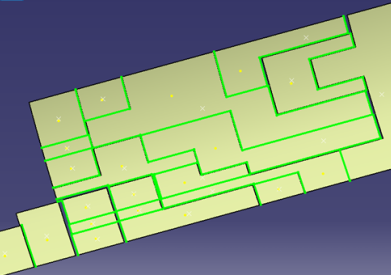
-
Click OK to validate and exit the dialog box.
The iso-thickness areas group and the iso-thickness areas are created.
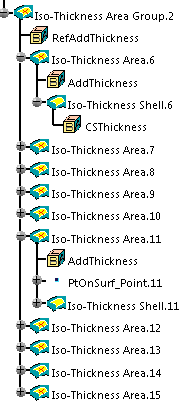
The contour of the iso-thickness area is relimited by the bottom of the
ramp
(i.e. last ply+1 on ramp support) if the plies are created with the
grid approach
(i.e. if they are based on ramp support).
In that case,
the iso-thickness area turns yellow.
If the iso-thickness area cannot be
relimited by the bottom of the ramp, it turns pink (unless you chose to
ignore the ramp supports).
A
warning is issued if an iso-thickness area needs to be reworked.
You can
modify the shape of an iso-thickness area before creating the solid.
When the core sample point of an iso-thickness area may have become
invalid,
a mask at the iso-thickness area node indicates that the
feature needs to be updated.
If you modify an iso-thickness area, and
add or modify core sample points,
iso-thickness areas that have not been
impacted do not need to be recomputed.
|
-
Double-click the iso-thickness areas group to edit it.
-
Double-click an iso-thickness area to edit it.
Bottom
of slope computation with Ramp Support
cuve only prevents
the relimitation of iso-thickness
area
shell by recomputed bottom curves, i.e.
when ramp supports curves could not be
used.
Point indication and
Point selection are the same as
described in the main dialog box.
Additional thickness ratio defines an
additional thickness as a ratio of
thickness similar to
the one in group
panel but specific to current iso-thickness
area. |
Right-click an Iso-Thickness Shell to
access its contextual menu
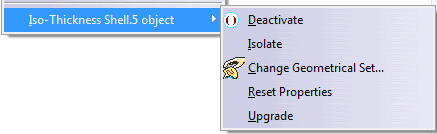
|
 |