 |
This task shows you how to swap the skin, i.e. to project the contours
of plies from an engineering surface to a manufacturing surface. |
 |
- Skin swapping can be performed only on tangency continuous
shells.
- When a Swapping feature already exists, you cannot create
a second one, but you can edit it if modifications are required.
-
Butt Splice Zones
are taken into account by the Skin Swapping command if you select
the Stacking node.
- If the Skin Swapping was applied to elements under
the staking, you can generate a Skin Swapping feature for the
Butt Splice Zones by selecting either a zone or its group.
In
this case a Skin Swapping feature will be added at the end of the
Composites Geometry of the corresponding elements.
|
 |
Open the
SKinSwapping1.CATPart document. |

|
-
Click Skin Swapping
in the Manufacturing toolbar.
-
Select the feature where you want to insert the swapping
in the specification tree.
-
Now select the manufacturing surface to be swapped with
Extrude.1:
Select Offset.1 in Body.1.
Its name is displayed in the dialog box in the With column.
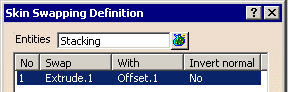
The draping direction is displayed in the 3D geometry.
 |
You can click Invert
to reverse the draping direction and be consistent with the direction
defined in the engineering plies.
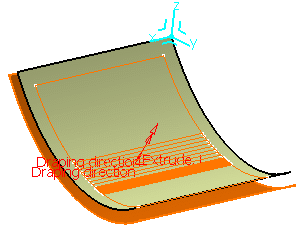 |
|
|
-
Select the Swapping mode (we have kept
Projection).
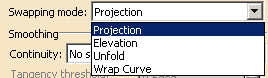
If the data before swapping skins are:
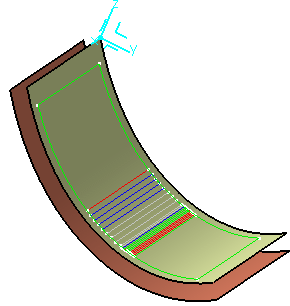
- Projection: The command performs a projection
perpendicular to the destination surface.
The projection of the
engineering geometry of the ply from the engineering surface to the
manufacturing
surface is only performed on the nearest portion of
the manufacturing shell.
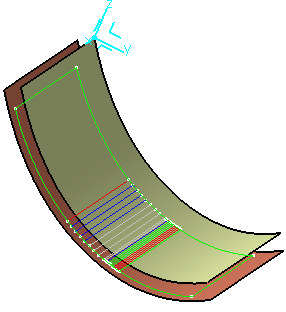
- Elevation: The command performs a projection
perpendicular to the origin surface.
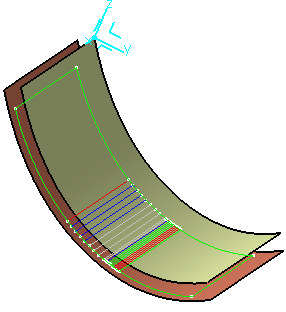
- Unfold: This option provides a complete flatten view
of the Composite plies that will be then
put in actual shape during
manufacturing.
The resulting contour is the exact same result as a
geometry transfer between the folded and the unfolded surface.
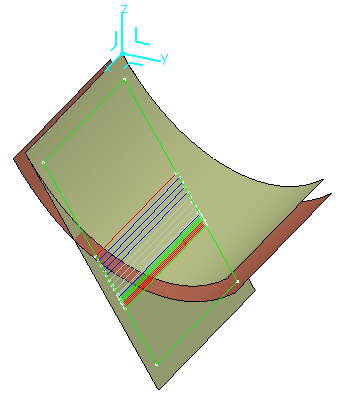
The surface supporting the selected plies must be an unfolded
surface of the destination surface,
or the destination surface must
be an unfolded surface of that supporting the plies.
If this is not
the case, selection is not possible and an error message is
displayed.
The unfolded surface must have been created with
Surface type set to All
- Wrap Curve: See Swapping the Skin with Wrap Curve.
|
|
|
-
Set the Smoothing parameters:
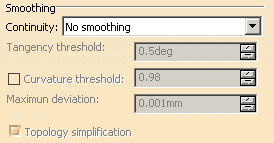
- Select a Continuity type, that is the
correction mode for the smoothing,
then the corresponding
parameters:
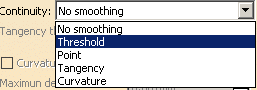
-
No
smoothing: This is the default mode.
-
Threshold: The tangency and curvature
thresholds options are taken into account.
-
Point:
No point discontinuity should remain.
-
Tangent: No tangent discontinuity should remain.
The
tangency threshold option is not taken into account, it is grayed
out and the defined value is ignored.
-
Curvature: No curvature discontinuity should remain.
The
curvature threshold option is not taken into account, it is grayed
out and the defined value is ignored.
In case tangent or curvature discontinuities remain, an
error message is issued. |
When a curve is curvature
continuous and you try to smooth it, a warning message
informs you that there is no discontinuity to smooth.
|
- Set the Tangency threshold, that is the tangency discontinuity value
below which the curve is smoothed.
If the curve presents a tangency discontinuity greater than this threshold, it is not smoothed.
- Check Curvature threshold
to set the curvature discontinuity value above which the curve is smoothed.
- Define a Maximum deviation
value to set the allowed deviation between the initial curve and the
smoothed curve.
Therefore, the resulting smoothed curve fits into a pipe which radius is
the maximum deviation value and the center curve is defined by the
selected curve.
|
-
If you have selected a stacking, a plies group or a
sequence, the Invert stacking order check box is available.
Select this check box to invert the order of plies during the swapping (we
have not selected this check box:
- If you have selected a stacking:
- The order of plies groups is inverted (the first
becomes the last, the second becomes first before last, etc.),
- Then, in each plies group, the order of sequences is
inverted in the same way,
- Then in each sequence, the order of the plies is
inverted in the same way.
- If you have selected a plies group:
- The order of sequences is inverted (the first becomes
the last, the second becomes first before last, etc.),
- Then in each sequence, the order of the plies is
inverted in the same way.
- If you have selected a sequence:
- The order of plies is inverted (the first becomes the
last, the second becomes first before last, etc.).
|
-
Click OK in the Skin swapping dialog box.
The engineering geometry is transferred
onto the manufacturing surface.
It is put in the No show space on the
engineering surface.
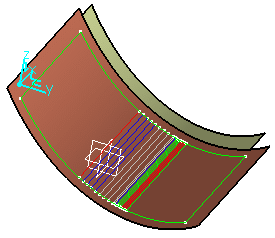
In the specification tree, the Swapping feature
(identified as Swapping.xxx) is displayed under each ply.
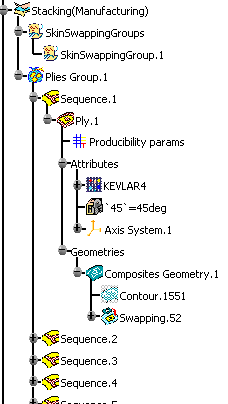
|
 |
You can edit any swapping element in order to change the
manufacturing surface.
-
Double-click Swapping.1 element in the
specification tree.
-
The Skin Swapping Definition dialog box is displayed.
-
Select the new manufacturing surface.
-
Click OK to perform the modification.
-
Only the ply referencing the feature is modified.
|
 |
You can also change the manufacturing surface by editing a
plies group.
-
Double-click the Plies Group.1 feature in the
specification tree.
-
The Plies group definition dialog box is
displayed.
-
Click Change. Click No in the message box to
edit the existing swapping. The Skin swapping dialog box
is displayed.
-
Select the new manufacturing surface.
-
Click OK to perform the modification.
|
 |