 |
This task
shows you how to create a surface stamp by specifying the various
geometrical parameters of the punch: |
|
|
|
Creating a Surface Stamp
|
 |
Open the
NEWStamping4.CATPart document from the samples directory.
If you use the Aerospace SheetMetal Design workbench, open the
Aero_Stamping4.CATPart document. |
 |
-
Click Surface Stamp
.
The Surface Stamp Definition dialog box opens, providing default
values. |
|
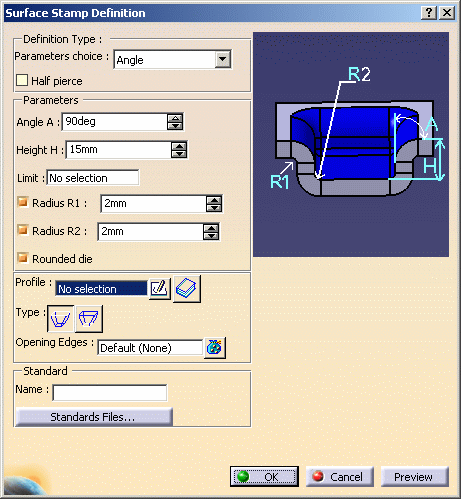 |
|
-
In the specification tree, select
Sketch-for-Surface-Stamp, the profile previously defined.
-
Change the value in the different fields, if needed.
In our example, we chose the following values: |
-
Angle A: 90deg
-
Height H: 15mm
-
Radius R1: 2mm
-
Radius R2: 2mm
|
The surface stamp is previewed. |
|
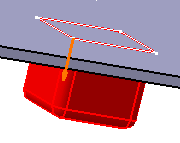 |
|
-
Click Preview to compute the surface stamp.
-
Click OK to validate.
The surface stamp (identified as
Surface Stamp.1) is created and the specification tree is updated
accordingly. |
|
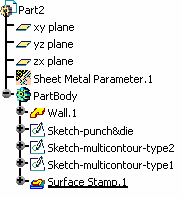 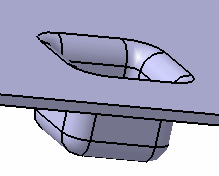 |
|
|
|
|
|
Creating a Surface Stamp without Fillets
|
|
By default, Radius R1, Radius R2 and Rounded
Die are activated.
This means that all edges of the surface stamp are filleted. |
|
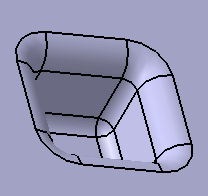 |
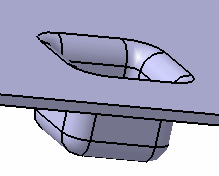 |
|
- Rounded Die lets you create a surface stamp which die's edges are all
filleted.
If you click to clear the Rounded Die check box, the surface stamp
should look as shown below. |
|
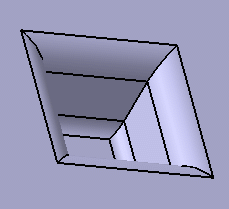 |
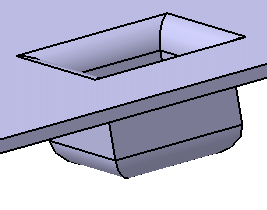 |
|
- The Radius R2 lets you create fillets on the surface stamp's bottom.
If you click to clear the Radius R2 check box, the Rounded Die check box
is automatically cleared as well and the surface stamp should look as shown
below. |
|
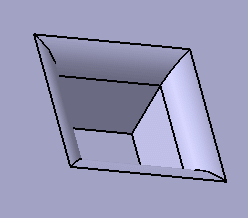 |
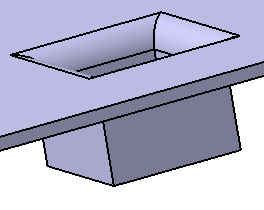 |
|
- The Radius R1 lets you create fillets on the surface stamp's top.
If you click to clear the Radius R1 check box but keep Radius R2 and
Rounded die selected, the surface stamp should look as shown below. |
|
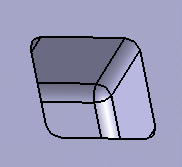 |
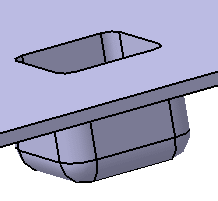 |
|
You can also disable Radius R1 and Radius R2
if you want to create the surface stamp without a fillet. |
|
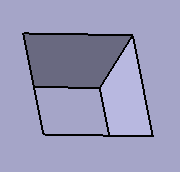 |
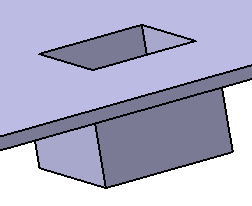 |
|
 |
 |
Creating a Surface Stamp with any Sketch
|
|
-
Create a sketch on a different plane.
-
Click Surface Stamp
.
The Surface Stamp Definition dialog box opens, providing
default values.
Note: The sketch represents the bottom of the stamp. The Upward
sketch profile option in the Type field is disabled.
-
Change the value in the different fields, if needed.
In our example, we chose the following values:
- Angle A: 85deg
- Height H: 60mm
- Radius R1: 2mm
- Radius R2: 2mm
The surface stamp is previewed.
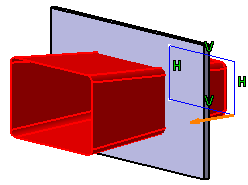
 |
- The angle and the height of the punch are
calculated with respect to the plane of the
sketch.
- The stamp will be built only when the punch
intersects the part body.
|
|
|
-
Click Preview to compute the surface stamp.
The stamp is relimited when it intersects the part body.
The orange arrow indicates the direction of the stamp. |
-
Click OK to validate.
The surface stamp (identified as Surface Stamp.xxx) is created
and the specification tree is updated accordingly. |
|
|
|
|
|
Creating a Surface Stamp with a Limiting Plane
|
|
-
Double-click Surface Stamp.1 in the specification tree to
edit it.
-
In the Surface Stamp Definition dialog box, right-click
in the Limit field.
-
In the contextual menu, select Create Plane.
The Plane Definition dialog box is displayed.
-
Select the xy plane in the specification tree as
reference.
The offset from the plane and its direction is previewed.
 |
- To be able to use a limiting plane for a stamp, the profile of
the stamp must be based on a sketch.
- The limiting plane has to be parallel to the sketch plane. If
not, an error message is displayed.
|
-
Use the up and down arrows to change the offset value.
In our scenario, we selected an offset of 25mm. |
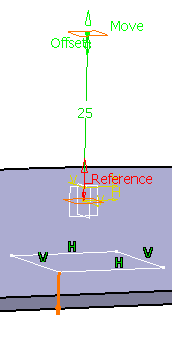 |
-
If needed, click Reverse Direction to change
the offset direction.
-
Click OK to close the Plane Definition
dialog box.
The stamp based on the limiting plane is previewed. |
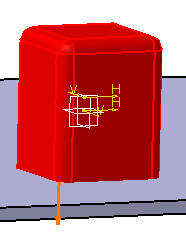 |
 |
Should you need to delete or edit the plane you previously
selected, right-click the Limit field and select the
appropriate item in the contextual menu. |
|
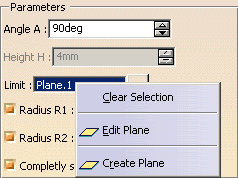 |
|
For more information on planes, refer to
Creating Planes in
Generative Shape Design User's Guide. |
 |
You will note that the Height field is deactivated.
This is due to the fact that the height of the stamp is now based on
the distance between the stamping point and the plane which is
coincident with the external face of the stamp. |
-
Click Preview to compute the surface stamp.
-
Click OK to close the Surface Stamp Definition
dialog box.
The stamp is created. |
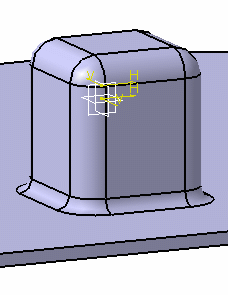 |
|
|
Creating a Surface Stamp with Opening
Edges
|
|
-
Double-click Surface Stamp.1 in the specification tree to
edit it.
-
In the Surface Stamp Definition dialog box, click the
Opening Edges field to activate it.
-
On the geometry, select one opening edge as shown below.
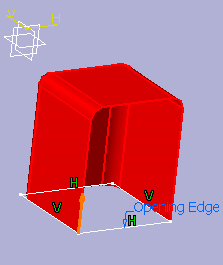 |
- You can select several opening edges.
- If you want to delete your selection, right-click on the
Opening Edges field and select Clear Selection in the
contextual menu.
|
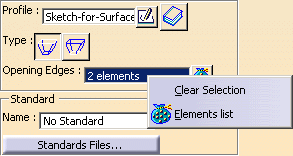 |
Should you need to modify the opening edges:
- right-click on the Opening Edges field and select Elements
list in the contextual menu and use the Remove or
Replace button to change your selection.
or
- click the icon at the right of the field, then use the
Remove or Replace button to change your selection.
|
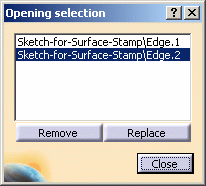 |
|
-
Click Preview to compute the surface stamp.
-
Click OK to create the stamp with opening
edges.
|
|
Inserting a Profile from a Catalog
|
|
-
Click Surface Stamp
.
The Surface Stamp Definition dialog box opens, providing default values.
-
Change the value in the different fields, if needed.
In our example, we chose the following values: |
-
Angle A: 90deg
-
Height H: 10mm
-
Radius R1: 1mm
-
Radius R2: 1mm
|
-
Click catalog
to select a stamp feature
from the catalog.
The Catalog Browser dialog box is displayed. |
-
If needed, browse to the directory where the stamp
catalog is filed.
In our example we selected Aero_Sheetmetal_Cutouts catalog. |
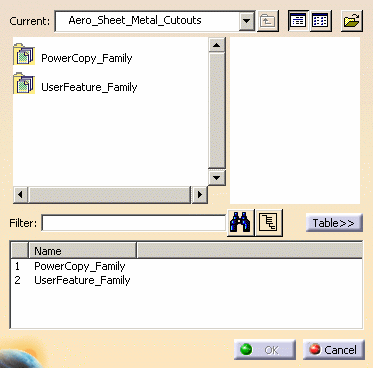 |
|
-
Double-click on UserFeature_family.
The features available in the catalog are displayed. |
|
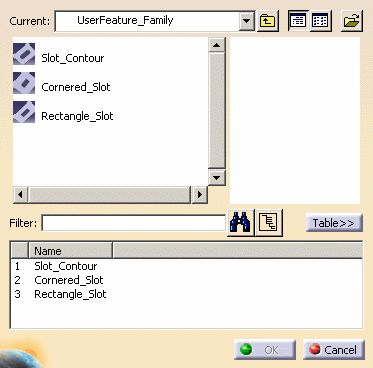 |
-
Select Slot_Contour and click OK to close the
catalog browser.
-
On the geometry, select the inputs needed to insert the
feature:
-
Use Wall.1 or Web.1 as Reference plane;
-
Use Point.1 as Reference point;
-
Use an edge of Wall.1 or Web.1 as Reference axis.
|
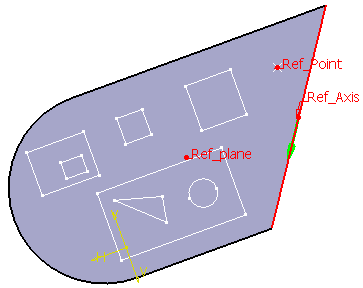 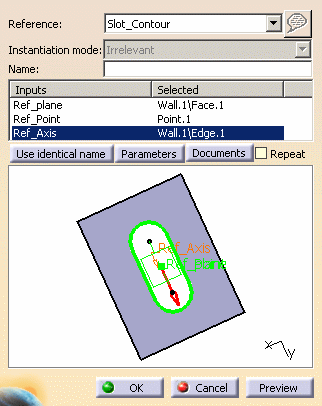 |
|
-
Click OK to insert the feature.
-
Click Preview to compute the surface stamp.
-
Click OK again to create the stamp.
|
|
 |
Creating a Stamp Based on a Multi Contour
Profile
|
|
Applying parameters to the top of the surface
stamp
|
|
-
Click Surface Stamp
.
-
In the specification tree, select
Sketch-multicontour-type1
The Surface Stamp Definition dialog box opens. |
-
Select Angle as Definition type and the first type of
stamp .
-
Change the value in the different fields, if needed.
In our example, we chose the following values: |
-
Angle A: 90deg
-
Height H: 10mm
-
Radius R1: 2mm
-
Radius R2: 2mm
|
The surface stamp is previewed. |
|
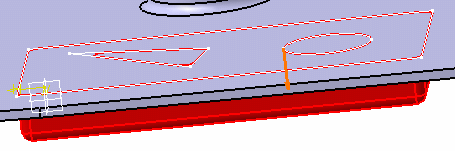 |
|
-
Click Preview to compute the surface stamp.
-
Click OK to validate.
The surface stamp with several inner
contour (identified as Surface Stamp.2) is created and the
specification tree is updated accordingly. |
|
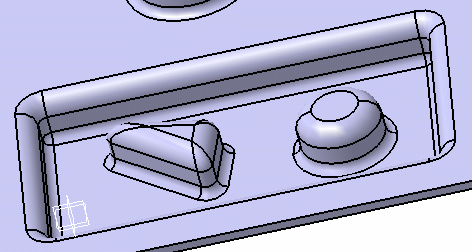 |
|
|
Applying parameters to the bottom of the
surface stamp
|
|
-
Click Surface Stamp
.
-
In the specification tree, select
Sketch-multicontour-type2
The Surface Stamp Definition dialog box opens. |
-
Select Angle as Definition type and the second type of
stamp 
-
Change the value in the different fields, if needed.
In our example, we chose the following values: |
-
Angle A: 60deg
-
Height H: 13mm
-
Radius R1: disabled
-
Radius R2: disabled
|
The surface stamp is previewed. |
|
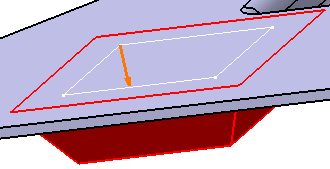 |
|
-
Click Preview to compute the surface stamp.
-
Click OK to validate.
The surface stamp with several inner
contour (identified as Surface Stamp.3) is created and the
specification tree is updated accordingly. |
|
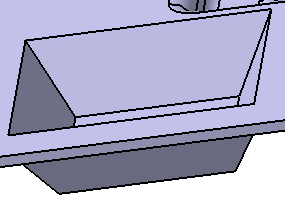 |
|
 |
The outer contour of the profile creates the outside portion of the stamp,
while the other contours (provided that they are not inside each other)
form the inner side of it.
|
 |
Creating a Stamp Based on a Punch and Die
Profile
|
|
-
Click Surface Stamp
.
-
In the Surface Stamp Definition dialog box, select
Punch and Die as Definition type.
-
In the specification tree, select Sketch-punch&die
The Surface Stamp Definition dialog box opens. |
-
Change the value in the different fields, if needed.
-
In our example, we chose the following values:
-
Height H: 13mm
-
Radius R1: disabled
-
Radius R2: disabled
|
A light preview is displayed. |
|
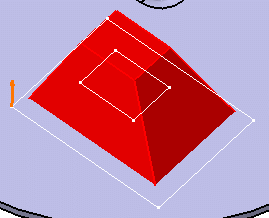 |
|
-
Click Preview to compute the surface stamp.
-
Click OK to validate.
The surface stamp with two
contours (identified as Surface Stamp.4) is created and the
specification tree is updated accordingly. |
|
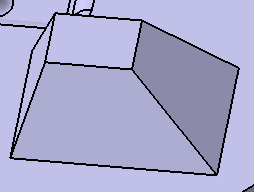 |
|
 |
Each punch edge must be parallel to the corresponding die edge. |
|
|
|
 |
|
|
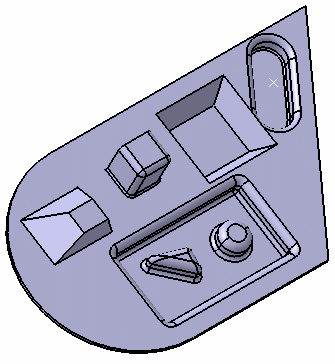 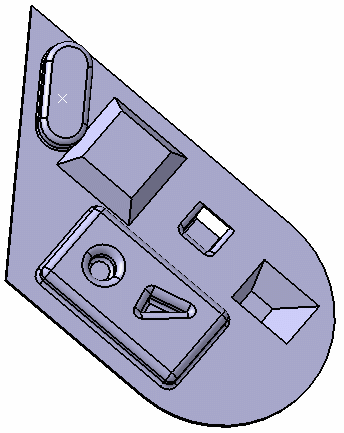 |
|
|
Creating a Stamp Based on a 3D Curve
|
|
-
Open the
NewStamping12.CATPart document. If you use the Aerospace SheetMetal
Design workbench, open the
Aero_Stamping12.CATPart document.
The part contains a simple 3D curve profile and a 3D multicurve profile.
-
Click Surface Stamp
.
-
In the specification tree, select Folded curve.2.
The Surface Stamp Definition dialog box opens.
-
Select Angle as Definition type and the first type of
stamp .
-
Change the value in the different fields, if needed.
In our example, we chose the following values: |
-
Angle A: 90deg
-
Height H: 6mm
-
Radius R1: 2mm
-
Radius R2: 2mm
|
-
Click Preview to compute the surface stamp,
then click OK to validate.
-
Click Surface Stamp
.
-
In the specification tree, select Folded curve.1.
The Surface Stamp Definition dialog box opens.
-
Select Angle as Definition type and the first type of
stamp .
-
Change the value in the different fields, if needed.
In our example, we chose the following values:
-
Angle A: 90deg
-
Height H: 6mm
-
Radius R1: 2mm
-
Radius R2: 2mm
|
-
Click Preview to compute the surface stamp,
then click OK to validate.
|
|
Creating a Two Profile Stamp
|
|
-
Open the
NewStamping9.CATPart document.
-
Click Surface Stamp
.
-
In the Surface Stamp Definition dialog box, select
Two Profiles as Definition type.
-
Check to deactivate Rounded Die.
-
In the specification tree, select Sketch.2 as first
profile and Sketch.3 as second profile.
 |
- If you want to define the internal part of the stamp, use the
Inner type
.
- If you want to define the external part of the stamp, user
the Outer type
.
|
-
Click Preview to compute the stamp.
You are warned that the stamp cannot be built. |
-
Start coupling sketches together selecting points.
You should end up with six couplings. |
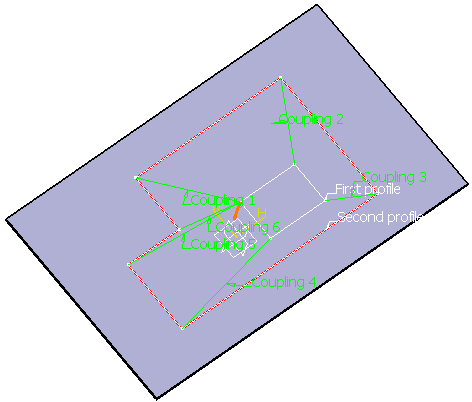 |
Once the coupling is done, the stamp can be computed and is
previewed. |
|
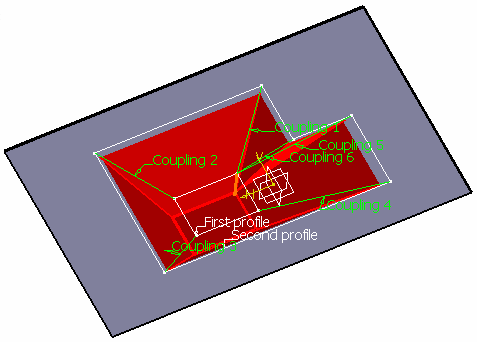 |
-
Click OK to create the stamp.
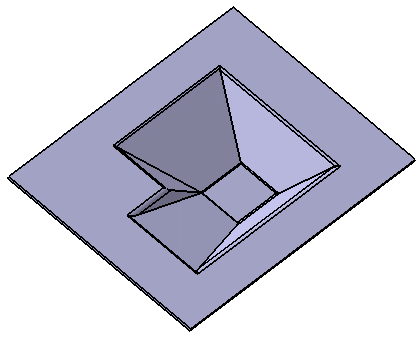 |
|
 |
Avoid as much as possible a coincidence between the edge of the
sketch profile and the edge of the base feature. Instead, let the
sketch profile exceed the edge of the wall. |
|
|
 |
|
|
 |