 |
-
Click
Producibility for Forming
.
Select
TunnelPlies-Convex under TunnelForming as the Plies
group. The plies are listed in the same order as in the plies
group. Rows named Die, Interface and Punch are added to visualize
results such as sliding (Sliding is a property of interfaces between
plies).
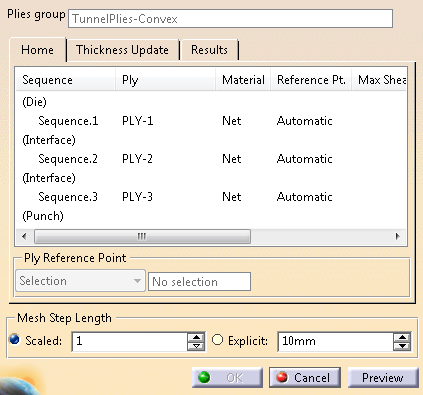
-
Select PLY-1.
In the list under Ply Reference Point, select
Selection. Select Selection Point
(Producibility) under Forming-Simulation > FLATTEN
PLANE. Repeat for each ply. Other options are:- Indication:
Pick a location in the graphic area.
- Automatic: The reference point is the
geometric center of the ply.
|
-
A mesh will be created.
Under Mesh Step Length, select Explicit and enter 8mm.
Mesh
Step Length is used to compute the simulation mesh. It can be: -
Scaled: The step length is a ratio computed from
the size of each ply.
- Explicit: You enter a value.
|
-
Click Preview.
- The simulation is run separately on each ply.
- The maximum shear and maximum deviation for each ply are
listed in the table
|
-
Go to
Results. Select a ply under Selection to start its
post-processing. -
To analyze the amount of shear resulting from the forming simulation:
- Under Display Result, select Shearing
angle from the list.
- Under Display Geometry, select
Producibility Mesh.
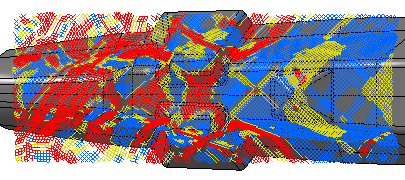
|
-
Select Deviation from the list to analyze the amount of deviation
between the actual and theoretical fiber directions.
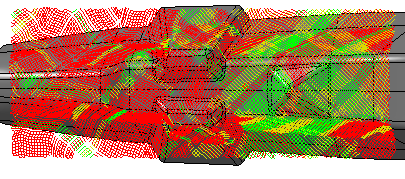 -
To analyze the amount of sliding that occurs during the forming process:
- Select an interface between two plies.
- Select Sliding from the list.
- Select Vectors under Display Geometry.
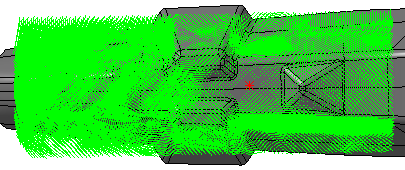
|
-
Validate to store the quick forming simulation, as Forming
under the plies group. -
After a modification of the model shape:
- Double-click Forming.
- Click Preview to update the simulation.
- Review the model as explained above.
|
|