 |
-
Click Shell
.
The Shell Definition dialog box is displayed. |
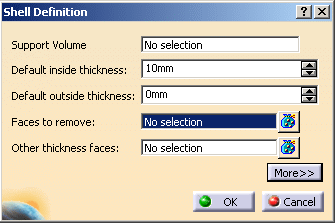 |
-
Select the Face to remove.
The Support Volume field is filled with the volume
owning the selected face. |
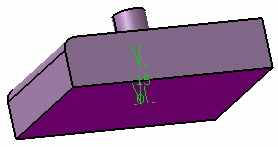 |
-
Enter 15mm in the Default inside thickness
field.
-
Click OK.
The feature is shelled: the selected face is left open. |
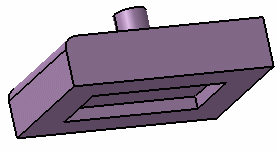 |
This element (identified as Shell.xxx) is added to the
specification tree. |
-
Double-click the shell to edit it.
-
Click the Other thickness faces field.
-
Select a face.
-
Double-click the thickness value displayed on this face.
-
In the dialog box that appears, enter 10mm and click
OK.
The length between the selected face and the shell is
now 10mm. |
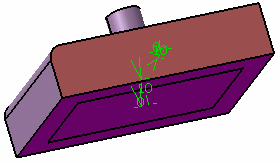 |
-
Click More>>.
-
Select the
Smoothing mode under the Deviation
parameters section.
 |
There are
three
types of smoothing modes:
- None:
No smoothing is applied. This is the default option. The Max
deviation field and Constant thickness
option are disabled.
-
Manual:
Allows you to enter a maximum deviation. The default value
is 0.1 mm. The Constant thickness
option is enabled to allow you to apply a constant
thickness.
-
Automatic:
Smoothing is applied automatically. The Max Deviation field is grayed out.
However, the Constant thickness option is enabled to allow you to apply a constant thickness.
|
-
Click OK.
 |
For further information about
shells, please refer to Creating Shells in Part Design
documentation. |
|