 |
This task shows you how to create a surface, or a set of surfaces, by
offsetting an existing surface, or a set of surfaces.
It can be any type of surface, including multi-patch surfaces resulting
from fill or any other operation. |
|
This task also deals with:
|
 |
Open the Offset1.CATPart
document. |
|
-
Click Offset
.
The Offset Surface Definition dialog box appears. |
-
Select the Surface to be offset.
An arrow indicates the proposed direction for the offset. |
-
Specify 200mm as the Offset value.
-
Click Preview
to preview the offset surface.
The offset surface is displayed normal to the reference surface.
|
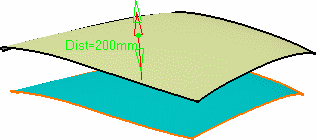 |
-
Click OK to create the surface.
The surface (identified as Offset.xxx) is added to
the specification tree. |
|
 |
- Depending on the geometry configuration and the offset value,
an offset may not be allowed as it would result in a debased
geometry. In this case, you need to decrease the offset value or
modify the initial geometry.
- When you modify an input value through
the dialog box, such as the offset value or the direction, the
result is computed only when you click Preview or
OK.
- Parameters can be edited in the 3D
geometry. To have further information, refer to the
Editing Parameters chapter.
|
|
|
|
|
Setting Optional Parameters
|
|
- You can display the offset surface on the other side of the
reference surface by clicking either the arrow or the Reverse
Direction
button.
|
 |
- You can define a smoothing type on the offset surface:
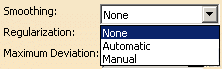 |
- None: the smoothing is constant. This is
the default type.
- Automatic (you can use the
Offset3.CATPart
document): a local smoothing is applied only if the constant offset
cannot be performed. It cleans the geometry of the surface and
enables the offset.
A warning box is launched and the modified surface is
shown in the 3D geometry. If a surface still cannot be
offset, no smoothing is performed and a warning message is
issued (as in the constant offset mode). If you click Yes,
erroneous sub-elements are removed and
the offset operation goes on. |
- Manual: a local smoothing is
applied as in the Automatic type. You need to define a Maximum
Deviation below which the elements are to be offset. If the
resulting deviation is greater than the defined deviation, no
smoothing
is performed and a warning message is issued (as in the constant offset
mode). If you click Yes, erroneous sub-elements are
removed and the offset operation goes on.
 |
- The deviation should be comprised between 0.001mm and the
Offset value (-0.1mm). For instance, if the Offset value is 20mm,
the maximum deviation is 19.9mm.
- The Maximum Deviation field is only available with
the Manual smoothing type.
|
|
 |
- You can select the Regularization type on the
offset surface:
- Local: The
Local regularization option regularizes the offset
surface by adding local modifications to the offset
surface. Therefore, using this option, the deviation between the
offset surface and the surface to be offset is
minimized. This option improves the robustness of the
offset computation.
- Global: The Global
regularization option regularizes the offset surface
completely. The same deviation is applied everywhere. If
the local regularization fails, by default, the offset
surface is globally regularized.
 |
The Regularization option
is available only with Automatic and
Manual smoothing type. |
|
|
- generate two offset surfaces, one on each side of the reference
surface, by checking the Both sides option.
|
|
- create several offset surfaces, each separated from the initial
surface by a multiple of the offset value, by checking the
Repeat object after OK option.
Simply indicate in the Object Repetition
dialog box
the number of instances that should be created and click OK. |
Remember however, that when repeating the offset it
may not be allowed to create all the offset surfaces, if it leads to
debased geometry. |
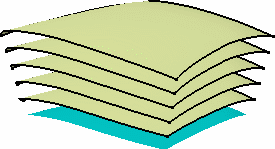 |
 |
If Both sides and Repeat object after OK are checked,
only the first offset surface will be repeated. |
|
|
- Would the value be inconsistent with the selected geometry, a warning
message is displayed, along with a warning sign onto the geometry.
If you move the pointer over this sign, a longer message is
displayed to help you continue with the operation. |
Furthermore, the manipulator is locked, and you need to modify
the value within the dialog box and click Preview. |
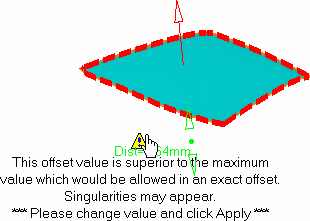 |
|
|
|
|
Removing Sub-Elements
|
|
The Sub-Elements to remove tab helps you
for the analysis in case the offset encounters a problem. |
|
Open the
Offset2.CATPart document. |
|
-
Perform steps 1 to 3.
-
Click Preview.
The Warning dialog box appears, the geometry shows the erroneous
sub-elements, and flag notes
display
sub-elements to remove.
 |
- There are different colored flag notes to display the
severity of errors:
 |
The red-colored flag shows that error is
critical. |
 |
The yellow-colored flag depicts warning. |
 |
The white-colored flag shows information
regarding the offset. |
- The exact location of errors can be easily pointed out
by arrow-heads of flag notes.
|
|
-
Click Yes to accept the offset.
In the Offset Surface Definition dialog box, the Sub-Elements to
remove tab lists the erroneous sub-elements and a preview of the
offset is displayed. |
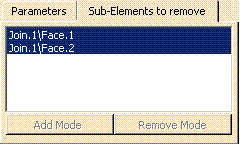
Important:
- This list is stable at update but not always
when you create a new offset. As a consequence, the
erroneous sub-elements in the list may be different.
|
|
 |
-
If you move the
mouse over a flag note, a longer message giving an accurate
diagnosis is displayed.
-
You can remove a
sub-element by right-clicking it and choosing Clear
Selection from the contextual menu.
|
|
As this list is not always optimal, you can manually add or remove
sub-elements:
- Add Mode:
- when you click an unlisted element in the geometry, it is
added to the list
- when you click a listed element, it remains in the list.
|
- Remove Mode:
- when you click an unlisted element in the geometry, the
list is unchanged
- when you click a listed element, it is removed from the
list
|
 |
If you double-click Add
Mode or Remove Mode, the chosen mode is
permanent, i.e. successively selecting elements will add/remove
them. However, if you click only once, only the next selected
element is added or removed. You only have to click the button
again, or click another one, to deactivate the mode. |
|
|
 |
The
list of sub-elements to remove is updated each time an element is
added.
Note that if you modify an input in the
Offset dialog box, the list is re-initialized. However, this list
is not re-initialized if the offset parameter is modified
directly from the tree by double-clicking Offset under
Offset.xxx. This means that you will have to reselect the
surfaces under the Sub-Elements to remove tab.
|
 |
The availability of context commands depend on the location
where you activate the contextual menu, and the context commands
act only on the lines that you right-click. If more than one
lines are highlighted, right-clicking one highlighted line is
equivalent to right-clicking all the highlighted lines at the
same time. In this case, the context command acts on all the
highlighted lines. Consider the following cases:
Case 1: line 1 is highlighted and line 1 is right-clicked: the
selected contextual command will act on line.
Case 2: line 1 is highlighted and line 2 is right-clicked (but
not highlighted): the selected contextual command will act on
line 2.
Case 3: line 1 and line 2 are highlighted and line 1 is
right-clicked: the selected contextual command will act on both
line 1 and line 2.
Case 4: line 1 and line 2 are highlighted and line 3 is
right-clicked (but not highlighted): the selected contextual
command will act on line 3.
|
 |
You can select the Automatically
Computes Sub-elements To Remove check box to automatically
compute and remove sub-elements. Use this check box to obtain a
better result after a modification of the offset parameter of
the offset feature.
In this case, the Sub-elements to remove list is not
available for manually adding or removing the sub-elements. |
|
-
Click Preview.
The offset surface is displayed normal to the reference surface. |
-
Click OK to create the surfaces.
The surfaces (identified as Offset.xxx) are added to the
specification tree. |
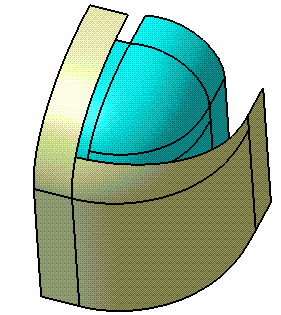 |
|
|
Performing a Temporary Analysis
|
|
While in the Offset command, you can perform a
temporary analysis in order to check the connections between surfaces or
curves. |
 |
Open the
Offset4.CATPart document. |
 |
-
Perform steps 1 to 3 (set 20mm as the Offset value).
-
Click Preview.
The Temporary Analysis icon is available from the Tools toolbar. |
-
Click Temporary Analysis mode
.
-
Select the analysis to be performed in the Analysis
toolbar by clicking either Connect checker
or Surfacic Curvature Analysis
.
-
Click OK in the Connect checker or
Surfacic
Curvature Analysis dialog box.
 |
You must activate the temporary
analysis mode before running any analysis. Otherwise, a persistent
analysis will be performed.
The Temporary Analysis node is displayed in the specification tree
and the associated analysis (here, Surfacic Curvature Analysis.1)
appears below: |
|
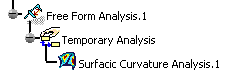 |
 |
- The analysis is not persistent. Thus when you click OK
in the
Offset Surface Definition dialog box to
create the curve, the
Temporary Analysis node disappears from the specification tree.
- An option is available from Tools > Options to let
you automatically set the analysis as temporary. Refer to the
Customizing section.
|
|
|