This section gives you information about the computation
process.

How are element stresses computed?
Element stresses at Gauss points are the product of the
Comportment Law and the Strain Deformation.
-
is the element stress
-
is the Comportment Law, computed as a function of the following
parameters, where:
-
is the Poisson Ratio
-
is the Young's Modulus
-
is the Strain deformation, computed according to the displacement.
For example, with a 2D displacement:
where
and
are the two partial derivatives. |
|

How are contact elements computed?
-
It is assumed that contact property is non-linear (of the
form K.X = F(X) ).
Nevertheless, in the particular case of contact without friction, the
solution is unique: it does not depend on the path used to put the two
geometries in contact.
Static solutions inside the Generative Part Structural
Analysis (GPS) product are thus solved with an iterative algorithm which
could be qualified by an "advanced linear" approach. At each computation step, local contact
directions are not updated (contrary to non-linear solvers). But if the
local curvature is small (compared to contact area width), this
approximation remains reliable and gives good results.
The contact connection mesh is done between overlapping
surfaces at their initial position. The solver does not take into account
large relative sliding between surfaces in contact. Contact condition is
only valid for elements connected by the mesh part.
|
-
In case of contact with
friction: after each contact iteration, the friction effects are
computed and the contact computation is launched again.
The computation uses a simplified Coulomb friction model.
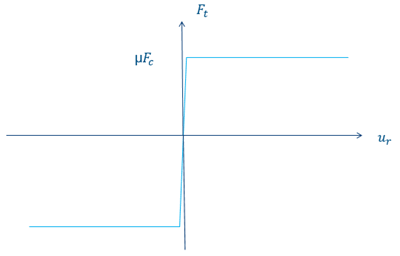
The high slope near the y-axis is due to the initial high stiffness (not infinite).
Springs are added to keep the friction ratio small while maintaining contact. For the
first iteration, there is no spring stiffness. The solver is started, and we determine Fc
(contact force) and Dt (tangential displacement). The tangential stiffness Kt
is added or updated.
The second iteration adds a high stiffness. Later iterations use Ft= Kt*Dt.
If Ft > µ*Fc/Ft, test for convergence.
If the solution is not converged, restart the solver and redetermine Fc and Dt.
|
-
To solve contact problems, an additional stiffness is added to
the contact element.
Adding stiffness may influence displacements, especially in the case of
two solids that are not really in contact.
For example: consider two surfaces (S1 and S2) with 2mm distance between.
Enforced displacements (dS1) are applied to S1:
dS1 = -0.5mm.
|

How are shell elements computed?
The average normal vector is used for shell elements.
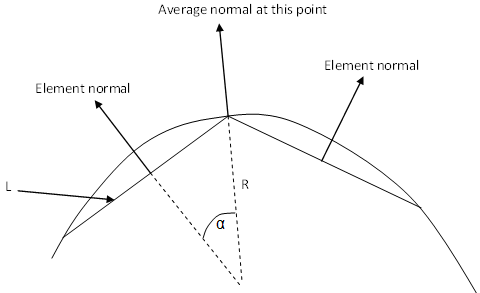
where:
- L is the element length.
-
is the angle between the element normal and the average normal.
- R is the estimated curvature radius

When the angle between the element normal and the
average normal is smaller than the shell normal tolerance and if the ratio between the
curvature radius and the thickness is greater than two, the average
normal is used instead of the element normal for all the shell elements
(TR3, TR6, QD4, QD8).
The default value of the shell normal tolerance is 20 degrees and its
value can be set using the ELF_Shell_Normal_Tol environment
variable. See Singularity Computation. |

How are node stresses computed?
Node stresses are extrapolations of element stresses.
The method consists in defining a continuous stress field
within the element:

where:
|
These nodal stresses values are obtained using the least
square minimization method:
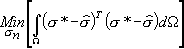
where
are the stresses computed with the finite element method from the nodal
displacements. |
|

How is error computed?
There are two steps in the error computation:
-
Stress smoothing.
This method consists in computing a weighted nodal
stress value at each nodes. |
 |
For more information about the nodal stresses values,
refer to How are node stresses computed? |
-
Error estimation.
Once the nodal stresses values have been found, a
continuous stress field is defined for each element:

where:
The error for each element (local error) is:

where:
The total error (Estimated Precision) is the sum of
all the local errors:
And the Global Estimated Error Rate is:
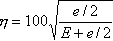
where
is the global strain energy. |
|
|

How are result and computation files
managed?
You can manage analysis results (contained in
.CATAnalysisResults files) and analysis computations (contained in
.CATAnalysisComputations files):
You can also customize analysis default external storage
(computation and result data) settings.
For more details, refer to
External Storage. |