 |
This task shows you how to create core samples to drill the part at one
or several spots to retrieve the laminate. The core samples are computed on
the whole design or on a selection of plies groups. The result is stored in
the design and is associative with the input.
|
 |
Available in Composites Engineering Design (CPE) and Composites Design for Manufacturing (CPM).
The core samples can be
edited during their creation, or after. Once you have generated the core samples from a reference entity such as
a grid, grid virtual stacking, zone group or plies group, the point location
can only be modified manually.
|
 |
Open the MultipleCS01.CATPart
document. Follow the instructions displayed when you double-click older
core samples to migrate them to this new version. Il you do not migrate
them, you still can read them. |
 |
Creating Core Samples
-
Click
Multiple Core Sample
in the Analysis toolbar. The Multiple Core Sampling
dialog box opens.
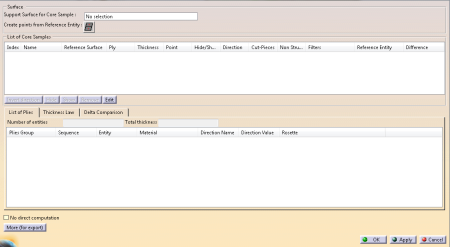
-
Select
the Support Surface for Core Sample. You can select
either a surface of a plies group.
- Selecting a plies group reverts to selecting its associated surface.
All the plies of the plies group found along the normal to
its surface will be processed.
- If the selected surface is not that associated to the
plies group, points selected on this surface are processed
as follows:
- The first plies group found is represented by the
yellow lines (plies) and the purple line (its reference
surface).
- The selected surface is shown in red.
- The blue arrow points to the selected point.
- The dotted green arrow shows its projection on the
reference surface of the first plies group found.
- The green line is the normal to the reference
surface of the plies group at the projection of the
selected point.
- Multiple Core Samples processes all the
plies of that plies group along this line.
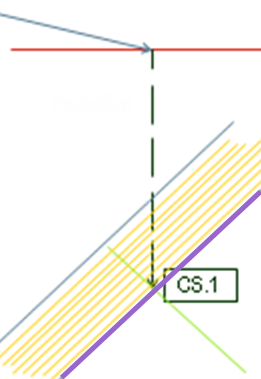
|
-
Optional: Select the No direct computation check box.
- No computation is done when you add points, until
you click Apply.
- As a consequence, the Results table is not
updated until you click Apply.
|
Pick points directly in the graphic area to create
the core samples. The core samples are added to the list.
-
Alternatively, click Create points from Reference
Entity.
Select a reference entity in the dialog box that opens. It
can be:
- A grid or a virtual stacking: A point is created at
the center of each cell of the grid.
- A zone group: A point is created at the center of each
zone.
If the zone contains a transition zone, the point
is created on the portion with no transition zone, meaning
it is not the exact center.
- A plies group: A point is created in each surface with a
constant thickness area.
If you have selected a plies group, define the width or the
areas to consider. Either key in a value, or measure the
distance between two plies using the contextual menu.
Click OK.
- The core samples are created and listed under List
of Core Samples, with their details.
- Associativity between the core samples and the reference
entity is managed by manual edition.
- If you have selected a grid, virtual stacking or a zone
group, they are listed under Reference Entity.
|
Under
List of Core Samples, select one
or several lines to edit their information.
- Index is the order of core samples. Use
the green arrows to modify it.
- Name is the name of the core sample. Click a
name to edit it.
- Ply is the name of the ply found under the
point. It is not editable.
- Thickness is the value of the laminate found
under the point. It is not editable.
If the considered
plies group insersets another one, the thickness is computed
on both plies groups. In such a case, the thickness is not
accurate, but still relevant.
- Point is the name of the point you have
picked. It is not editable.
- Hide/Show indicates the visibility status.
Click either Hide or Show to change
the status.
- Direction can be Normal (to the
surface) or Invert. Click Invert direction
in the dialog box or the arrow in the graphic area to modify
it.
- Cut-Pieces, Non Struct Plies and
Filters are the options selected for the core
samples as you picked the points.
- Reference Entity. This column is filled with
the name of the entity previously selected if you had
entered a zone group, a grid or a grid virtual stacking.
- Difference.
If you select one core sample, information is displayed under
Results. Results is inactive if you
select several core samples.
You are ready to do one of the following.
|
-
Alternatively, click Edit.
-
Click Invert Direction, Hide, Show,
Remove to modify the direction, the visibility status or
delete the core samples.
-
Check the results (disabled if you have selected several core samples).
Under List of Plies, the details of the plies:
- Number of entities
- Total thickness
- Plies group
- Sequence
- Entity
- Material
- Direction name
- Direction Value
- Rosette
Under Thickness Law, the details of the thickness
law of the core sample:
- Material
- Thickness law as a number of plies and
percentage for each direction
- Total number of plies for each direction, if there is
more than one material.
Under Delta Comparison:
- Material
- Delta
- Details of the directions
- Status of the delta
- Status of the thickness
- Total Delta Difference
- Thickess difference between the core sample and the
reference entity.
|
-
Optional: Select
More (for export) to access export
options.
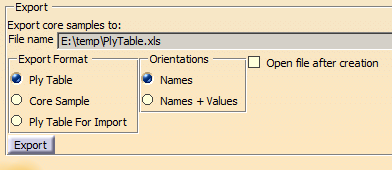
- Click ... to enter the name of the exported file.
- Select the Export Format.
- Decide if you want to export the Names, or the
Names+Values of the Orientations.
- Optional: Select the Open file after creation
check box.
- Click Export to create the exported file.
Examples of :
- Ply Table
Reference Geometry Ply Group Sequence Ply/Insert Material CS.1 CS.2
Extrude.1 PG.1 Sequence.1 Ply.1 KEVLAR4 90
Extrude.1 PG.1 Sequence.2 Ply.2 KEVLAR4 -45
Extrude.1 PG.1 Sequence.3 Ply.3 KEVLAR4 0
Extrude.1 PG.1 Sequence.4 Ply.4 KEVLAR4 45
Extrude.1 PG.1 Sequence.5 Ply.5 KEVLAR4 90
Extrude.1 PG.1 Sequence.6 Ply.6 KEVLAR4 0
Extrude.1 PG.1 Sequence.7 Ply.7 KEVLAR4 -45
Extrude.1 PG.1 Sequence.8 Ply.8 KEVLAR4 45
Extrude.1 PG.1 Sequence.9 Ply.9 KEVLAR4 90 90
Extrude.1 PG.1 Sequence.10 Ply.10 KEVLAR4 -45 -45
Extrude.1 PG.1 Sequence.11 Ply.11 KEVLAR4 45 45
Extrude.1 PG.1 Sequence.12 Ply.12 KEVLAR4 0 0
DIR 0 1 3
DIR 45 1 3
DIR -45 1 3
DIR 90 1 3
Total Crossed Entities 4 12
Thickness 0.8mm 2.4mm
Core Sample Points X Y Z
CS.1 139.578205mm -10mm 14.228437mm
CS.2 -92.186211mm -10mm 17.124897mm
All plies are listed by their name. The plies with multiple
intersections, if any, are listed at the end, the number of
multiple intersections is given for each ply concerned.
- Core Sample
Core Sample CS.1 139.578205mm -10mm 14.228437mm
Ply Group Sequence Ply/Insert Material Direction Rosette
PG.1 Sequence.12 Ply.12 KEVLAR4 0 Rosette_SP
PG.1 Sequence.11 Ply.11 KEVLAR4 45 Rosette_SP
PG.1 Sequence.10 Ply.10 KEVLAR4 -45 Rosette_SP
PG.1 Sequence.9 Ply.9 KEVLAR4 90 Rosette_SP
DIR 0 1
DIR 45 1
DIR -45 1
DIR 90 1
Total Crossed Entities 4
Thickness 0.8mm
Core Sample CS.2 -92.186211mm -10mm 17.124897mm
Ply Group Sequence Ply/Insert Material Direction Rosette
PG.1 Sequence.12 Ply.12 KEVLAR4 0 Rosette_SP
PG.1 Sequence.11 Ply.11 KEVLAR4 45 Rosette_SP
PG.1 Sequence.10 Ply.10 KEVLAR4 -45 Rosette_SP
PG.1 Sequence.9 Ply.9 KEVLAR4 90 Rosette_SP
PG.1 Sequence.8 Ply.8 KEVLAR4 45 Rosette_SP
PG.1 Sequence.7 Ply.7 KEVLAR4 -45 Rosette_SP
PG.1 Sequence.6 Ply.6 KEVLAR4 0 Rosette_SP
PG.1 Sequence.5 Ply.5 KEVLAR4 90 Rosette_SP
PG.1 Sequence.4 Ply.4 KEVLAR4 45 Rosette_SP
PG.1 Sequence.3 Ply.3 KEVLAR4 -45 Rosette_SP
PG.1 Sequence.2 Ply.2 KEVLAR4 -45 Rosette_SP
PG.1 Sequence.1 Ply.1 KEVLAR4 90 Rosette_SP
DIR 0 3
DIR 45 3
DIR -45 3
DIR 90 3
Total Crossed Entities 12
Thickness 2.4mm
The plies are listed in the order they have been processed,
which makes the multiple intersections more visible, if any.
- Ply Table For Import
(CPG stands for CutPieceGroup
and CP for CutPiece)
PlyGroup Sequence Ply CPG CP Material Direction Rosette Surface Draping Ply ID CS.1 CS.2
PG.1 Sequence.1 Ply.1 KEVLAR4 90 Rosette_SP Extrude.1 F 1 90
PG.1 Sequence.2 Ply.2 KEVLAR4 -45 Rosette_SP Extrude.1 F 2 -45
PG.1 Sequence.3 Ply.3 KEVLAR4 0 Rosette_SP Extrude.1 F 3 0
PG.1 Sequence.4 Ply.4 KEVLAR4 45 Rosette_SP Extrude.1 F 4 45
PG.1 Sequence.5 Ply.5 KEVLAR4 90 Rosette_SP Extrude.1 F 5 90
PG.1 Sequence.6 Ply.6 KEVLAR4 0 Rosette_SP Extrude.1 F 6 0
PG.1 Sequence.7 Ply.7 KEVLAR4 -45 Rosette_SP Extrude.1 F 7 -45
PG.1 Sequence.8 Ply.8 KEVLAR4 45 Rosette_SP Extrude.1 F 8 45
PG.1 Sequence.9 Ply.9 KEVLAR4 90 Rosette_SP Extrude.1 F 9 90 90
PG.1 Sequence.10 Ply.10 KEVLAR4 -45 Rosette_SP Extrude.1 F 10 -45 -45
PG.1 Sequence.11 Ply.11 KEVLAR4 45 Rosette_SP Extrude.1 F 11 45 45
PG.1 Sequence.12 Ply.12 KEVLAR4 0 Rosette_SP Extrude.1 F 12 0 0
DIR 0 1 3
DIR 45 1 3
DIR -45 1 3
DIR 90 1 3
Total Crossed Entities 4 12
Thickness 0.8mm 2.4mm
Core Sample Points X Y Z
CS.1 139.578205mm -10mm 14.228437mm
CS.2 -92.186211mm -10mm 17.124897mm
|
-
Click OK to create the core samples and exit the dialog box. The core samples are created as
CS.x under a Core Sample
Group under Review Tools.
-
Double-click the Core Sample Group or an
individual core sample to edit them.
|
|
Editing Core Samples
-
In the Multiple Core Samples dialog box:
- Select one or several core samples under List of
Core Samples and click Edit.
- Or double-click one core sample in the graphic area.
- Or double-click one or several core samples in the
specification tree under a core sample group.
- Or right-click one or several core samples in the
specification tree under a core sample group and select
Definition in the contextual menu.
The Core Sample dialog box opens. Its
content varies with the selection. The Reference Surface
is the support surface selected in the main dialog box.
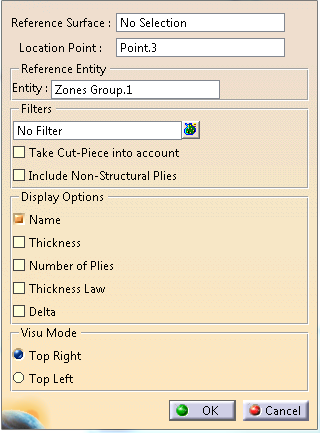 |
Optional: Change the location point.
This is not possible when several core samples have been selected.
-
Select a Reference Entity to compare the core
sample thickness law with.
- If you have created the core samples from a
reference entity, this entity is proposed.
- If you have selected several core samples with the same
reference entity, its name is displayed.
- If you have selected several core samples with several
reference entities, Multiple CS is displayed.
|
-
Optional: Under Filters, click
to select the impacted entities.
- Either select them manually.
- Or click
in the dialog box that opens to select them with the
Stacking Management.
If you have selected several core samples with the same
filter, its name is displayed. If you have selected several
core samples with several filters, Multiple CS is
displayed. The Filters column is updated for this
line.
|
-
Optional:
Select the Take Cut-Piece into account check box to take them
into account, if any. -
Optional: Select the Include Non-Structural Plies check box
too take them into account, if any. -
Under Display Options, select the required ones:
When you start the edition:
- The information on core samples is displayed with the
current options.
- An option is selected if all selected core samples share
that option.
- A star before an option means several core samples have
a different status for this option.
- Select an option with a star to apply it to all
selected core samples.
- Click (i.e. select and deselect) an option with a
star twice to remove it from all selected core samples.
Note that Delta starts the computation of the comparison to
find the delta. The core sample information is updated in the
graphic area. If you change the composites parameters,
the changes are not taken into account automatically. You need
to edit the core samples and uncheck/check the box.
|
-
Under Visu Mode, select the required option, i.e. where the
information is displayed. When you start the edition, an option is
selected if it is shared by all selected core samples. When you
select an option, it is applied to all selected core samples. -
When available and required, select Show Core Sample Results
to display them. Alternatively, right-click one core sample in the
specification tree under a core sample group, and select Core
Sample Results in the contextual menu. |
 |