 |
-
Click Flanged Hole
.
-
Click the surface where you want to place the hole.
A grid is displayed to help you position the
flanged hole.
The Flanged Hole Definition dialog box is displayed,
providing default values.
Notes:
- The image in the right-hand pane of the dialog box is
updated as you choose your parameters and options, and
provides a graphical explanation about the current
selection.
- The options available in the dialog box are updated
according to the items selected in the Definition Type
area.
|
-
If you want to use a standard, click the Standard
File button and browse to select a standard file. In this case, the
standard parameters will be used, and you do not need to (and cannot)
specify the definition type, flanged hole parameters and/or flat
pattern diameter (depending on what exactly is specified in the
standard file); go directly to step 8.
 |
- The parameters that are driven by the standard table cannot be
modified.
- For more information on standard files, refer to Editing the
Sheet and Tool Parameters, and to Customizing Standard Files to
Define Design Tables in the Customizing chapter of this user's
guide.
|
For the purpose of this scenario, do not select a
standard file, and proceed with step 4.
-
Choose the diameter that should be dimensioned from the
Parameters choice list:
-
Specify whether the flanged hole should be created
without a cone (i.e. only with the filleted portion of the flanged hole)
or with a cone (i.e. with the filleted portion of the flanged hole and
with a cone).
Note that selecting the Without cone option
has the following consequences:
-
The Height H field is disabled, the height
being automatically computed in this case.
-
Deactivating the Radius field is impossible,
because the radius value for the flanged hole external curvature must
be specified in this case.
-
Specify whether the flanged hole to be created with or
without a burring tap.
You can use design tables to define a burring tap. It is only available
if With cone is selected.
Notes: If you select With tap:
- The Radius R
box is disabled, the radius being automatically computed.
- The Flat Diameter
box is disabled and its value is equal to
Diameter D or
Diameter d depending on the
flanged hole type. The diameter value should be similar in both
folded and flat views.
- The support diameter is equal to the
Diameter d or
Diameter D value depending
on the flanged hole type.
- The support height is equal to height H.
|
 |
If the burring tap is created on non-planar surfaces, you
cannot generate an unfolded view in a drawing. |
-
To specify the burring tap, define the thread type and
parameters:
If you select Metric Thick Pitch
or Metric Thin Pitch:
- A Thread Description
box lists all available descriptions that use ISO standards.
- The Pitch value
depends on the selected description. The path for the standard
files is
win_b64\resources\standard\thread\Metric_Thick_Pitch.xml or
win_b64\resources\standard\thread\Metric_Thin_Pitch.xml.
Note: The thread diameter should be greater than the support
diameter.
|
-
Choose the flanged hole parameters:
-
In the Height H field, specify the height
value for the flanged hole. Use the icon next to the field to specify
the reference from which the height is defined:
or
.
-
In the Radius R field, specify the radius
value for the flanged hole external curvature. Use the
box next to the field to disable this option.
-
In the Angle A field, specify the angle
value for the flanged hole.
This option is not available for the Two Diameters
or Punch & Die parameters, as the angle is automatically
computed in these cases.
-
In the Diameter D field, specify the major
diameter value for the flanged hole.
This option is not available for the Minor
Diameter parameter, as the major diameter is automatically
computed in this case.
-
In the Diameter d field, specify the minor
diameter value for the flanged hole.
This option is not available for the Major
Diameter parameter, as the minor diameter is automatically
computed in this case.
|
|
-
Choose the flat pattern
diameter:
-
K factor: uses the K Factor to compute the
flat pattern diameter.
-
Flat diameter: lets you set your own flat
pattern diameter. If you select this option, you must enter a value in
the associated field.
 |
- Make sure that the flat pattern diameter does not exceed the
flanged hole external contour. Otherwise, it will be impossible to
create the flanged hole.
- Flanged holes that were created prior to R16, without the flat
pattern diameter specified, do not inherit from this functionality.
In this case, to specify the flat pattern diameter, you need to
delete and create the flanged hole again.
- If you want to be able to perform any operation (like a cutout)
on a flanged hole, you need to use the K factor option.
|
-
Click Preview to visualize the flanged hole.
-
Click OK to validate.
-
The flanged hole (identified as Flanged Hole.xxx) is
created and the specification tree is updated accordingly.
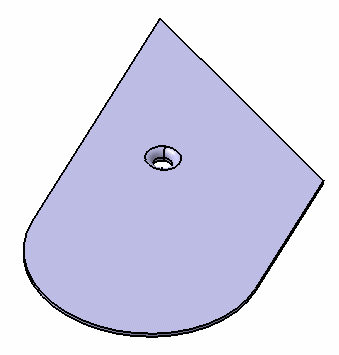 |
Flanged hole viewed from the front |
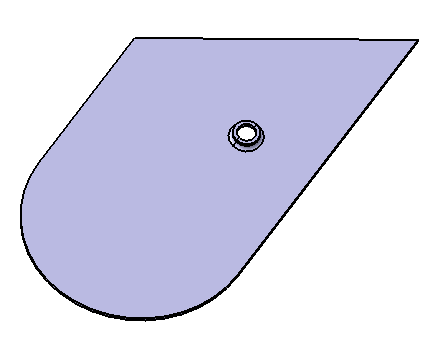 |
Flanged hole viewed from the back |
|