 |
This page explains how and when you should update your design. The
following topics are discussed:
Overview
The point of updating a part is
to make the application take your very last operation into account.
Although some operations such as confirming the creation of features
(clicking OK) do not require you to use the Update
command because by default the application automatically does it, some
changes to sketches, features etc. require the rebuild of the part.
To warn you that an update is needed, the application displays the
update symbol next to the part's name
and shows the
geometry in bright red.
Keep in mind that:
- To update the feature of your choice, just right-click that feature
and select Local Update.
- Besides the update modes, you can also choose to visualize the update
on the geometry as it is happening by selecting Activate Local
Visualization from the Tools > Options > Infrastructure
> Part Infrastructure, General tab. In this case, as
soon as you have clicked the Update icon
:
- the geometry disappears from the screen;
- each element is displayed as it is updated, including elements in
No Show mode. Once they have been updated, they remain in
No Show mode.
Two Update Modes
To update a part, the application provides two update modes:
What Happens When the Update Fails?
Sometimes, the update operation is not straightforward because for
instance, you entered inappropriate edit values or because you deleted a
useful geometrical element. In both cases, the application requires you to
reconsider your design. The following scenario exemplifies what you can do
in such circumstances. |
 |
Open the
Update3.CATPart document. |
|
-
Enter the Sketcher to replace the circular edge of the
initial sketch with a line, then return to Part Design.
The application detects that this operation affects the
shell. A yellow symbol displays on the feature causing trouble i.e. the
shell in the specification tree. Moreover, a dialog box appears providing
the diagnosis of your difficulties and the preview no longer shows the
shell:
To resolve the problem, the dialog box provides the following options. If
you wish to rework Shell.1, you can:
- Edit it
- Deactivate it
- Isolate it
- Delete it
|
|
 |
To
display the Parents and Children dialog box,
right-click a line in the dialog box and select Parents/Children
from the contextual menu.
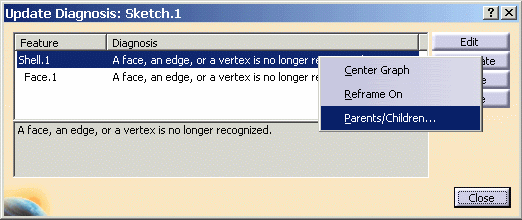 |
|
-
For the purposes of our
scenario that is rather simple, click Shell.1 if not already
done, then Edit. The Feature Definition Error window displays, prompting you to
change specifications. Moreover, the old face you have just deleted is
now displayed in yellow.
The
text Removed Face is displayed in front of the face, thus
giving you a better indication of the face that has been removed. Such a
graphic text is now available for Thickness and Union
Trim features too.
-
Click OK to close
the window. The Shell Definition dialog box appears.
-
Click the Faces to remove
field if not already done and select the replacing face.
-
Click OK to close the Shell Definition
dialog box and obtain a correct part. The shell feature is rebuilt.
|
|
Canceling Updates
You can cancel your updates by clicking the Cancel
button available in the Updating...dialog box. |
|
Interrupting Updates
This scenario shows you how to update a part and interrupt the update
operation on a given feature by means of a useful message you previously
defined. |
 |
Open the
Update.CATPart document and ensure that the manual update mode is on. |
|
-
Right-click Hole.1 as the feature from which
the update will be interrupted and select the Properties
contextual menu item.
The Properties dialog box is displayed.
-
Check the Associate stop update option. This
option stops the update process and displays the memo you entered in the
blank field. This capability is available in
manual or automatic update mode.
-
Enter any useful information you want in the blank field.
For instance, enter "Fillet needs editing".
-
Click OK to confirm and close the dialog box.
The entity Stop Update.1 is displayed in the specification
tree, below Hole.1, indicating that the hole is the last
feature that will be updated before the message window displays.
-
Edit Sketch.1, which will invoke an update
operation.
When quitting the Sketcher, the part appears in bright red.
-
Run the update operation by clicking the
icon.
The Updating... as well as the Stop Update message
windows are displayed. The Stop Update windows displays your
memo and lets you decide whether you wish to stop the update operation or
continue it.
-
Click Yes to finish.
The part is updated. You can now edit the fillet if you consider it
necessary.
|
 |
Using this capability in automatic update mode, the
Stop Update dialog box that displays is merely informative. |
|
-
If you decide not to use this capability any longer, you
can either:
- right-click Hole.1, select Properties and
check the Deactivate stop update option: the update you
will perform will be a basic one. To show that the capability is
deactivated for this feature, red parentheses precede Stop
Update.1 in the specification tree:
.
- right-click Stop Update.1 and select Delete
to delete the capability.
|
Update All Command
The Update All command synchronizes copied solids linked to
external references, but also updates the whole geometry of the part. For
more information about external references, see Part Design User's
Guide: User Tasks: Handling Parts: Handling Parts in a
Multi-Document Environment.
Sometimes, copied solids can be referenced by other features. For
example, an edge fillet can reference the edge of a copied solid. When
the copied solid is synchronized, its whole geometry can change
completely, making it impossible for the Replace mechanism to reroute
the edge fillet on an edge without doing it randomly.
Therefore in some cases, the Replace Viewer dialog box is
needed to specify on which sub elements, features that referenced sub
elements of the old solid geometry, are to be rerouted in the new
geometry. By using the arrows displayed in the dialog box, you can
change the way features use the orientation of the referenced geometry.
The Replace Viewer
dialog box is displayed only if manual rerouting is needed. It is not
displayed if the Replace mechanism can solve all its reroute issues
automatically. For example, during
the synchronization process of an external reference of a line, the
Replace Viewer dialog box is not displayed. Line is made up
of one fragment, therefore rerouting other features on the
geometry of the line is automatically done. A curve, on the other hand, can be made
up
of more than one fragment. If other features use the external
reference of the curve, the Replace Viewer dialog box
is displayed during the
external reference synchronization process. Thus, you can specify on
which fragment the other features are to be rerouted on. |