|
This task shows how to join
surfaces or curves.
This involves:
|
|
Open the
Join1.CATPart document. |
|
-
Click Join
.
The Join Definition dialog box appears. |
In Part Design workbench, the
Join capability is available as a contextual command named 'Create
Join' that you can access from Sketch-based features dialog
boxes. |
-
Select the surfaces or curves to be joined.
-
You can edit the list
of elements to be joined:
|
 |
If you double-click
Add Mode or Remove Mode, the chosen mode is
permanent, i.e. successively selecting elements will add/remove
them. However, if you click only once, only the next selected
element is added or removed.
You only have to click the button again, or click another one, to
deactivate the mode.
|
 |
The availability of context commands depend on the
location where you activate the contextual menu, and the context
commands act only on the lines that you right-click. If more than
one lines are highlighted, right-clicking one highlighted line is
equivalent to right-clicking all the highlighted lines at the same
time. In this case, the context command acts on all the highlighted
lines. Consider the following cases:
Case 1: line 1 is highlighted and line 1 is right-clicked: the
selected contextual command will act on line 1.
Case 2: line 1 is highlighted and line 2 is right-clicked (but not
highlighted): the selected contextual command will act on line 2.
Case 3: line 1 and line 2 are highlighted and line 1 is
right-clicked: the selected contextual command will act on both line
1 and line 2.
Case 4: line 1 and line 2 are highlighted and line 3 is
right-clicked (but not highlighted): the selected contextual command
will act on line 3.
|
-
Right-click the elements from the list and
choose the Check Selection
contextual command.
This lets you check whether an element to be joined
presents any intersection (i.e. at least one common point) with
other elements prior to creating the joined surface.
If this command is not launched, possible intersections will not
be detected. |
The Checker dialog box is displayed, containing the
list of domains (i.e. sets of connected cells) belonging to the
selected elements from the Elements To Join list. |
-
Click Preview.
- An Information message is issued when no intersection
is found.
|
- When an element is self-intersecting, or when several
elements intersect, a text is displayed on the geometry, where
the intersection is detected.
|
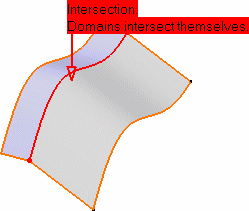 |
-
Click Cancel to return to the Join
Definition dialog box.
-
Right-click the
elements again and choose the Propagation options to allow the selection
of elements of same dimension.
- Distance Propagation: the tolerance
corresponds to the Merging
distance
value.
- Angular Propagation:
the tolerance corresponds to the
Angular Threshold value, if defined. Otherwise, it corresponds
to the G1 tolerance value as defined in the part.
|
Each new element found by propagation of the selected
element(s) is highlighted and added to the Elements To Join
list.
 |
Note that:
- The initial element to propagate cannot be a
sub-element,
- Forks stop the propagation,
- Intersections are not detected.
|
|
-
Click Preview in the Join Definition
dialog box.
The joined element is previewed, and its orientation
displayed. Click the red arrow to invert it if needed. |
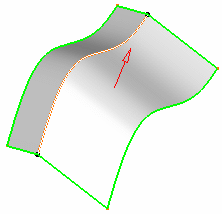 |
The join is oriented according to the first element in
the list. If you change this element, the join's orientation is
automatically set to match the orientation of the new topmost
element in the list. |
Using the check options
|
|
-
Check Check
tangency to find out whether the elements to be joined are
tangent. If they are not, and the option is checked, an error message is
issued when you click Preview and elements in error are highlighted in the 3D
geometry once you have clicked OK in the Update Error
dialog box.
 |
This option works for an
angular resolution of 0.5 degree. |
-
Check Check connexity
to find out whether the elements to be joined are connex. If they are
not, and the button is selected, an error message is issued indicating
the number of connex domains in the resulting join and elements in error
are highlighted in the 3D geometry.
 |
When clicking
Preview, the free boundaries are highlighted, and help you
detect where the joined element is not connex. |
-
Check Check manifold to find out whether the resulting join
is manifold.
-
You can check Simplify the result to
allow the system to automatically reduce the number of elements (faces
or edges) in the resulting join whenever possible.
-
You can check Ignore erroneous elements
to let the system ignore surfaces and edges that
would not allow the join to be created.
-
You can also
set the tolerance at which two elements are considered as being only one
using Merging distance.
 |
By default, the value is set to 0.001 mm and
corresponds to the value defined in Tools > Options. To
find out more about the merging distance value, refer to the General
Settings chapter. |
 |
It is not recommended to join two geometric elements with a merging
distance exactly equal to the distance between these elements. |
-
Check Heal merged cells to heal the
joined elements.
The value entered in the Merging distance box is taken into
account for healing. All the elements that have gap less than this value
are healed.
-
Check the
Angular Threshold option and specify the angle value below
which the elements are to be joined.
 |
If the angle value on the edge between two elements is
greater than the Angle Threshold value, the elements are
not joined. This is particularly useful to avoid joining overlapping
elements. |
 |
This option only applies to edges merged during the
join computation. To compute the angle, the middle of each merged
edge is taken into account. |
Removing Sub-Elements
|
-
Click the Sub-Elements To Remove
tab to display the list of sub-elements in the join.
These sub-elements are elements making up
the elements selected to create the join, such as separate faces of
a surface for example, that are to be removed from the join
currently being created.
You can edit the sub-elements list as
described above for the list of elements to
be joined. |
-
Check Create join with sub-elements
to create a second join, made of all the sub-elements displayed in the
list, i.e. those that are not to be joined in the first join.
 |
-
This option is
active only when creating the first join, not when editing it.
-
It is not available when the joined surface
belongs to an ordered geometrical set or a partbody created in
an hybrid environment.
-
A message is
displayed to inform you of the creation of a second join.
|
-
Click OK to create the joined
surface or curve.
The surface or curve (identified as Join.xxx) is added
to the specification tree. |
|
|
Sometimes elements are so close that it is not easy to see if they
present a gap or not, even though they are joined. Check the
Surfaces' Boundaries option from the Tools > Options >
General > Display > Visualization tab. |
|
 |
Using the Federation Capability
|
|
|
The purpose of the federation is to regroup several elements making up
the joined surface or curve that will be detected together with the
pointer when selecting one of them. This is especially useful when
modifying linked geometry to avoid re-specifying all the input elements. |
|
Open the
Join2.CATPart document. |
|
-
Create the join as usual, selecting all elements to be
joined.
(Make sure you do not select Sketch.1). |
-
From the Join Definition dialog box, click the
Federation tab, then select one of the elements making up the
elements federation (providing the No federation and All
propagation modes are not selected).
-
Choose a propagation mode, the system automatically
selects the elements making up the federation, taking this propagation
mode into account.
- No federation: no element can be selected
- All: all elements belonging to the resulting joined
curve/surface are part of the federation. Therefore, no element
can be explicitly selected.
|
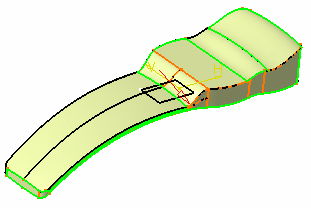 |
- Point continuity: all elements that present a point
continuity with the selected elements and the continuous
elements are selected.
|
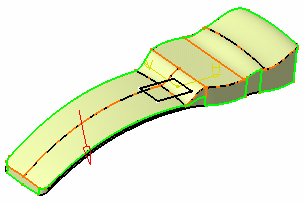 |
Tangent continuity: all the elements that
are tangent to the selected element, and the ones tangent to it, are
part of the federation. |
Here, only the top faces of the joined surface are
detected, not the lateral faces. |
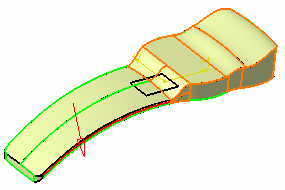 |
 |
To federate a surface and its boundaries
in tangency, you need to select the face as well as the edges: both
face and edges will be federated. |
- No propagation: only the
elements explicitly selected are part of the federation.
|
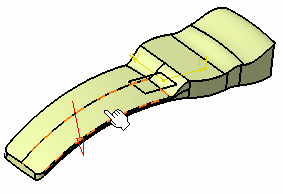 |
-
Choose the Tangency continuity propagation
mode.
-
Move to the Part Design workbench (select Start >
Mechanical Design > Part Design), select the Sketch.1, and click
Pad
to create an up to surface pad, using the joined surface as
the limiting surface.
-
Select the front edge of the pad, click Edge Fillet
and create a 2mm fillet.
-
Double-click Sketch.1 from the specification tree, then
double-click the constraint on the sketch to change it to 10mm from the
Constraint Definition dialog box.
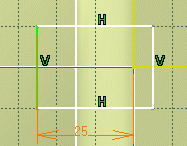 |
|
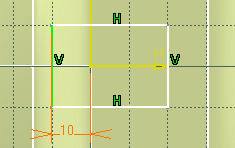 |
Sketch prior to modification lying over two faces |
|
Sketch after modification lying over one face only |
-
Exit the sketcher
.
The up to surface pas is automatically recomputed even though it
does not lie over the same faces of the surface as before, because
these two faces belong to the same federation. This would not be the
case if the federation including all top faces would not have been
created, as shown below. |
-
Double-click the joined surface (Join.1) to edit it, and
choose the No propagation mode.
-
Click OK in the Join Definition
dialog box.
A warning message is issued, informing you that an edge no longer
is recognized on the pad. |
-
Click OK.
The Update Diagnosis dialog box is displayed, allowing
you to re-enter the specifications for the edge, and its fillet. |
You then need to edit the edge and re-do the fillet to obtain the
previous pad up to the joined surface. |
-
Select the Edge.1 line, click the Edit button,
and re-select the pad's edge in the geometry.
-
Click OK in the Edit dialog box.
The fillet is recomputed based on the correct edge. |
|
 |
Remove Lost Edges Automatically |
|
If elements of a join feature have been replaced, you can remove them from
the Elements to join list in one step. |
 |
Open a part with a join feature, for example, a feature consisting of two
faces of a rectangular volume.
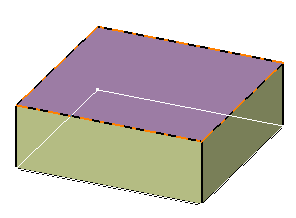 |
 |
-
In the specification tree, double-click the sketch, edit the
geometry, and exit the Sketcher workbench.
The pad is recomputed and the Update Diagnosis dialog box
appears.
Edges that are no longer recognized on the pad appear in the work area.
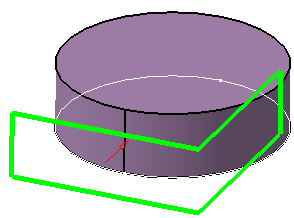 |
-
Select the Join.x
and click Edit.
The Feature Definition Error
panel appears. Do one of the following:
- Click Yes to remove all deleted sub-elements
from the Elements To Join list and select the
sub-elements again.
- Click No to preserve them and be able to edit
them manually.
|
|
|