|
The STEP interface provides a check of imported or exported content via
the validation properties. |
|
Check recommended practices, licensing and application protocol
requirements! Following validation properties are available: |
|
General Information
For each type of data, validation properties are specified
through the recommended practices.
The following validation properties are available:
- Geometric Validation Properties (GVP) for geometric exchange (at
part and assembly level)
- Assembly Validation Properties (AVP) for assembly structure
exchange (at assembly level)
- Annotation validation properties for 3D Tolerancing &
Annotation exchange (at part level)
- Validation Properties for User Defined Attributes
- Validation Properties for Composites.
For AP 242 XML files, GVP are used for geometry (.stp or .stpZ files)
and not for assembly (.stpx or .stpxZ). Assembly .stpx or .stpxZ files
support only AVP.
Validation properties are:
- Computed on the native data at export and are stored in the STEP
file,
- Computed on the imported data at import and compared with the
validation properties found in the STEP file. A status of comparison
is provided in the report file.
Validation Properties (VP) can be activated in Tools >
Options > STEP, under General.
Parameters becomes available to let you
select the options and set the parameters in the
Parameters for Validation Properties dialog box.
- Under Assemblies:
- Geometric Validation Properties (GVP)
GVP are not supported by STEP XML files.
- Or Assembly Validation Properties (AVP)
(recommended for assemblies, supported by
STEP XML files) according to your needs.
|
|
Geometric Validation Properties for 3D
Exact Geometry
Geometric Validation Properties can be used at several levels.
- Geometric Validation Properties are defined independently for
each class of geometry (solids/surfaces/curves), for each part, each
assembly node and each geometric element.
- Geometric Validation Properties for curves are supported at
assembly level.
- Geometric Validation Properties for bounding box are supported
at part level.
Validation Properties of Elements of a Part
At Export
The STEP file includes geometric validation properties for
- Each solid
- Centroid: Coordinates of the center of gravity
- Area: Area of the entity (wetted area for solids)
- Volume: Volume of the entity
- Each shell or surface
- Centroid: Coordinates of the center of gravity
- Area: Area of the entity
- Each contour or curve
- Centroid: Coordinates of the center of gravity
- Length: Length of the entity (applied to contour).
- The bounding box of the part
- It is defined by two points
and a diagonal in space.
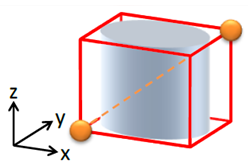
- Only the visible 3D elements
of the geometry are taken into account.
Annotations and axis systems are not taken into account.
- The edges of the bounding box are
parallel to the axes of the part coordinate system.
These properties are completed in the export report with the
estimation of their computation errors for each solid and each shell
at export and at import.
- The estimation of the computation error on the area or the
volume is provided as a relative value.
- The estimation of the computation error on the centre of
gravity is provided as an absolute value for each coordinate and
a bounding box of the entity.
Validation Properties of Elements of a Part
At Import
For each imported solid, shell, surface,
contour or curve and for the imported part as a
whole, the report file indicates the geometric validation properties
computed on the imported data, the GVP read in the STEP file and the
status of comparison between the two sets of GVP.
In addition, the report at import provides the GVP status and the
following error information computed on each imported solid or
shell.
- In most cases, the centroid deviation error that applies to
solid, shell, product or instance, is given as a percentage
based on the bounding box. However, when the deviation error is
under a threshold, it is given as a distance.
- The surface area difference value and error ratio apply to
solid, shell or product.
- Volume difference value and error ratio apply to solid or
product.
- The bounding box appears with the two
points and the diagonal in space shown above.
These properties are completed with the estimation of their
computation errors for each solid and each shell.
- The estimation of the computation error on the area or the
volume is provided as a relative value.
- The estimation of the computation error on the centre of
gravity is provided as an absolute value for each coordinate and
a bounding box of the entity.
Clouds of Points (COPS)
When standard
validation properties are not accurate enough, e.g. for aeronautic
long term archiving, COPS ensure that the archived data are
equivalent to the native data, within a given tolerance by comparing
any face with any check point lying on it.
- At export:
- The STEP file is enriched with COPS properties (i.e. a
cloud of points) for each exported face.
- These points are computed inside the face, on the
support of the face, or on the boundary of the face.
- The syntax of the STEP file respects the Recommended
Practices.
- At import:
- For each face, the COPS properties are read and the
distance between each point of the cloud and the support
surface of the face is computed.
- If the distance is greater than a user defined
tolerance, there is an error message in the err file.
Note:
- The check at import is reported only in the report and error
files.
- The repartition of the points in the face is automatic. A
high curvature generates many points.
- You cannot define an area to be controlled by COPS. The
whole product exported is checked.
- The unit used for geometric validation properties is the
STEP length user unit.
Validation Properties of a Part
The exported STEP file includes geometric validation properties
for a Part :
- Centroid: Coordinates of the center of gravity (applies to
solid, shell and contour)
- Area: Area of the entity (wetted area for solids) (applies
to solid and shell)
- Volume: Volume of the entity (applies to solid)
- Length: Length of the entity (applied to contour)
Validation Properties of an Assembly
When the option is selected the exported STEP file includes
geometric validation properties for Products and intances :
- Centroid: Coordinates of the center of gravity (applies to
product and instances)
- Area: Area of the entity (wetted area for solids) (applies
to product)
- Volume: Volume of the entity (applies to product).
Validation Criteria
The status of comparison for a given solid or shell or contour is
ok if:
- Ratios (Volume difference and Surface area difference and
Length difference) are lower than the user tolerance.
- And the centroid deviation is lower than the user tolerance,
or the ratio (centroid deviation versus entity size) is lower
than the user tolerance.
Extended STEP
Interface use the most relevant criterium: Ratio is
appropriate for large size models, while centroid deviation is
adapted for smaller models.
|
|
Geometric Validation Properties for 3D
Tessellated Geometry
Geometric Validation Properties can be used at several
levels. The check for area and centroid is performed according to
fixed tolerances.
Validation Properties of Elements of a
Part
Available validation properties are:
- For solid, shell or surface set
- Number of facets,
- Surface area,
- Centroid
- For wire or curve set
- Number of segments
- Total length
- Centroid
- For point set:
Validation Properties of a Part
Available validation properties are:
- Number of facets
- Surface area
- Number of segments
- Total length of all contours of the part
- Centroid of the part
- Bounding box (defined by two opposite points).
The centroid represents the centroid of facets if there are
solids, shells or surface sets. Otherwise it represents the
centroid of wire or curve, if any, otherwise it represents the
centroid of point sets.
Validation Criteria
They are:
- The maximum percentage of variation for volume, area,
length for solids, shells, contours and variation for
centroid deviation versus model size
- The maximum variation for centroid.
Note: For a centroid, a deviation higher than the maximum
variation is valid if the percentage of variation for the
centroid deviation versus the model size is lower than the
maximum percentage.
Examples
Below are some extracts of import report files.
- Curve
#176 Circle.2 Type: COMPOSITE_CURVE
Transferred correctly Computed Properties:
Length:3.544908e+mm - wire centroid:(0.000000 mm,10.000000
mm,0.000000 mm) Read Properties : Length:3.744908e+mm - wire
centroid:(0.000000 mm,10.000000 mm,0.000000 mm) Validation
failed : Error ratio: Length:5.641896% - wire centroid:0.000000%
/ 0.000000mm -
- Solid
#2614 PartBody Type: MANIFOLD_SOLID_BREP
transferred correctly Computed Properties:
Area:1.840000e+004 mm2 - Volume:1.200000e+005 mm3 -
Centroid:(-130.000000 mm,70.000000mm,10.000000 mm) -
Area:Relative Error:0.000% - Volume:Relative Error:0.000%
Centroid:Absolute Errors:(0.000 mm,0.000 mm,0.000 mm) - Box
sizes:(100.0 mm,60.0 mm,20.0 mm) Read properties:
Area:1.840000e+004 mm2 - Volume:1.200000e+005 mm3 -
Centroid:(-130.000000 mm,70;000000 mm,10.000000 mm) -
Validation successful: Error Ratio: Area:0.000000% -
Volume:0.000000% - Centroid: 0.000000% / 0.000000mm
- Surface with AP242 ed1
#335 Surface.1 Type:
OPEN_SHELL Transferred correctly Computed properties: Shell
Area:3.698668e+004mm2 - Shell Centroid:(-64.086136 mm,1.631528
mm,6.504039 mm) - Relative error:0.000% Centroid: Absolute
Errors:(0.000 mm,0.000 mm,0.000 mm) - Box sizes:(125.4 mm,260.2
mm,41.2 mm) Read Properties: Shell Area:3.698668e+004 mm2 -
Shell Centroid:(-64.086021 mm,1.631612 mm,6.504087 mm) -
Validation succesful: Error ratio: Shell Area:0.000227% - Shell
Centroid:0.000052% / 0.000150mm -
- Surface with AP 214
#197 Fill.1 Type:OPEN8SHELL
Transferred correctly Computed Properties:
Area:1.000000e+002 mm2 - Centroid:(0.000000 mm,10.000000
mm,0.000000 mm) - Area:Relative error:0.000% Centroid:Absolute
Error:(0.000 mm,0.000 mm,0.000 mm)- Box sizes:(0.0 mm,11.3
mm,11.1 mm) Read Properties: Area:1.000000e+002 mm2 -
Centroid:(0.000000 mm,10.000000 mm,0.000000 mm) - Validation
successful : Error Ratio: Area:0.000000% - Centroid: 0.000000% /
0.000000mm
- Part
Geometric Validation Properties at Part level:
Computed Properties: Area:1.840000e+004 mm2 - Shell
Area:3.698676e+004 mm2 - Volume:1.200000e+005 mm3 -
Length:2.049061e+003 mm - Centroid:(-130.000000 mm,70.000000
mm,10.000000 mm) - Shell Centroid:(-64.086136 mm,1.631528 mm,
6.540039 mm) - Wire Centroid:(12.11368 mm,58.306047 mm,-2.138570
mm) Bounding Box: Corner Points:(-180.00 mm,-132.36 mm,-66.35
mm)(107.23 mm,241.84 mm,87.94 mm) - Diagonal: 496.315883 mm
Read Properties: Area:1.840000e+004 mm2 - Shell
Area:3.698668e+004 mm2 - Volume:1.200000e=005 mm3 -
Length:2.049.61e+003 mm - Centroid:(-130.000000 mm,70.000000
mm,10.000000 mm) - Shell Centroid:(-64.086136 mm,1.631528 mm,
6.540039 mm) - Wire Centroid:(12.11368 mm,58.306047 mm,-2.138570
mm) Bounding Box: Corner Points:(-180.00 mm,-132.36 mm,-66.35
mm)(107.23 mm,241.84 mm,87.94 mm) - Diagonal: 496.315883 mm
Validation successful: Error Ratio: Area:0.000000% - Shell
Area:0.000227% - Volume:0.000000% - Length0.000000% -
Centroid:0.000000%/ 0.000000mm - Shell Centroid:0.000030% /
0.000150mm - Wire Centroid:0.000000% / 0.000000mm - Bounding
box:0.000000%
- Instance
Assemblage Composition:
Centroid:(-29.380994 mm,105.876987 mm,-111.474132 mm) - Centroid
read:(-29.380994 mm,105.876987 mm,-1411.474132 mm)
Validation successful: Centroid Position Error:0.000000 mm
- Assembly Product
#71 Composition1: Computed
Properties: Area:9.089815e+002 mm2 - Shell Area:1.000000e+002mm2
- Volume:2.000000e+003mm3 - Length:1.354491e+002 mm -
Centroid:(50.000000 mm,-0.000000 mm,10.000000 mm) - Shell
Centroid:(0.000000 mm,10.00000 mm,0.000000 mm) - Wire
Centroid:(-0.000000 mm,2.617152 mm,22.343627 mm) Read
Properties: Area:9.089815e+002 mm2 - Shell Area:1.000000e+002mm2
- Volume:2.000000e+003mm3 - Length:1.354491e+002 mm -
Centroid:(50.000000 mm,0.000000 mm,10.000000 mm) - Shell
Centroid:(0.000000 mm,10.000000 mm,0.000000 mm) - Wire
Centroid:(0.000000 mm,2.617152 mm,22.343627 mm) Validation
successful: Error Ration: Area:0.000000% - Shell Area:0.000000%
- Volume:0.000000% - Length:0.000000% - Centroid Position
Error:0.000000 mm - Centroid Shell Position Error: 0.000000 mm
Centroid Wire Position error:0.000000 mm -
- Maximum Errors
Geometric validation properties
check: OK Maximum errors: Centroid: #2614: 0.000000 mm
Volume: #2614: 0.000000 % Area: #2614: 0.000000 %
Length: #242 : 0.000000 % Shell centroid: #335: 0.000150 mm
Wire Centroid: #242: 0.000000 mm Shell Area: #335:
0.000227%
|
|
Annotation Validation Properties for
3D Tolerancing & Annotation
Annotations, also known as Product Manufacturing Information (PMI)
can be presented as polylines
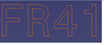
or as tessellated
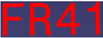
Validations properties apply to graphic annotations only.
Validation Properties of Elements of a Part
For the saved views (captures), they are:
- Number of annotations per saved view (capture)
For the polyline presentation, they are:
- Total length of the polylines representing each annotation
- Centroid of the polylines representing each annotation
- Affected geometry (AP 242 only).
For the tessellated presentation, they are:
- Total length of the lineic tessellations found in each
annotation
- Centroid of the lineic tessellations found in each
annotation
- Number of the lineic elements
- Total area of the surfacic tessellations found in each
annotation
- Centroid of the surfacic tessellations found in each
annotation
- Number of surfacic elements
- Affected geometry (AP 242 only).
Affected geometry contains:
- The area of the geometry linked to the PMI, if the geometry is a face (Affected area).
- The length of the geometry linked to the PMI, if the geometry is a curve (Affected curve length).
At import, the Affected Geometry properties are computed and
compared with the values found in the STEP file. The computed error is given as a percentage
in the report file. If this percentage exceeds 5%, the validation fails.
Export and import as both exact and tessellated are not supported.
Example
Computed Properties : Number of Facets:8 - Number of Segments:9 - Centroid:(-63.329167 mm,5.603107 mm,15.392448 mm) - Total area:4.221e+000 mm2 - Centroid of facets:(-89.998539 mm,5.603107 mm,10.004080 mm) - Total length:9.803e+001 mm – Affected area: 25.40000 mm2
Read Properties : Number of Facets:8 - Number of Segments:9 - Centroid:(-63.329168 mm,5.603107 mm,15.392448 mm) - Total area:4.221e+000 mm2 - Centroid of facets:(-89.998539 mm,5.603107 mm,10.004080 mm) - Total length:9.803e+001 mm - Affected area: 25.3900 mm2
Validation successful: Length Error:0.000000 mm - Area Error:0.000000 % - Number of segments Error:0 - Number of facets Error:0 - Centroid Position Error:0.000000 mm – Affected Area Error:0.040000 %
Validation Properties of a Part
They are: - Number of annotations
- Number of saved views (captures).
Example of validation properties of a part:
<>Expected number of annotations: 48, found: 48
Expected number of captures: 0, found: 0
Annotation Validation Properties Check: OK
|
|
Validation Properties for Graphic PMI |
|
Validation Properties for User Defined
Attributes
There are two types of validation properties for the
User Defined Attributes.
Validation Properties of Elements
For elements, they are:
- The counts of User Defined
Attributes for a given type of link, i.e. linked to a
solid or a shell.
- The counts of User Defined
Attributes for a given type:
- Real or measure with unit
- Integer
- String
- Boolean.
- Count of User Defined Attributes linked to a contour.
- Count of User Defined Attributes linked to a point.
At export, when a count is null, the validation property is not
exported in the STEP file. There are no trails of these validations
properties in the report file.
At import, when a validation property is found in the STEP file
or computed, a comparison status is provided in the report.
|
|
Composites
Validation Properties
Composites Validation Properties can be used at several levels.
Validation Properties of Elements of a Part
They are:
- Count of sequences (applies to a laminate table)
- Count of plies (applies to a sequence)
- Count of core (applies to a sequence)
- Count of cut pieces (applies to a ply).
Validation Properties of a Part
They are:
- Count of laminate tables
- Count of sequences
- Count of plies
- Count of cores.
|
|
Assembly Validation Properties
Assembly Validation Properties can be used at several levels
For each product having instances, the number of instances and a
notional centroid are stored in the STEP file as validation properties
at export and checked at import.
|
|
|