 |
-
Click CutOut
.
The Cutout Definition dialog box is displayed and the skin to be impacted
by the cutout is displayed in a different color.
-
Select a profile (sketch.1 in our example).
-
Click OK
in the Cutout Definition
dialog box.
The cutout is created. |
|
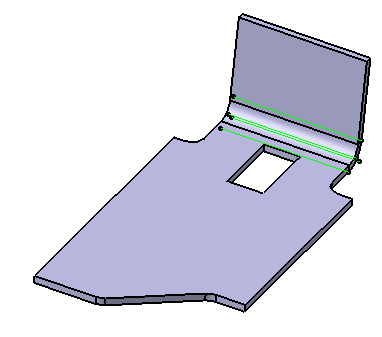 |
|
 |
Several end limit types are available:
-
Dimension: the
cutout depth is defined by the value measured along the direction.
-
Up to next: the
limit is the first face the application detects while extruding the
profile. This face must stops the whole extrusion, not only a
portion of it, and the hole goes through material.
-
Up to last: the
application will limit the cutout onto the last possible face
encountered by the extrusion.
|
-
In the specification tree, double click on Cut Out.1
to display the Cutout Definition dialog box.
-
Click More>> to display the maximum
information.
The Direction is already selected (Sketch.1), that is perpendicular to
the base feature.
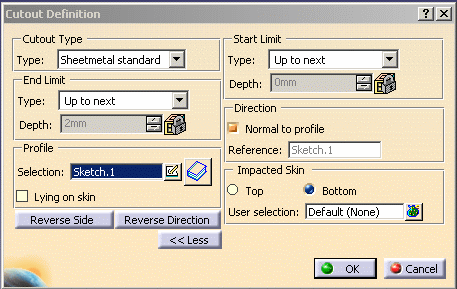 |
|
Here the Cutout's impacted skin is set to Default,
that is, the surface on which lies Sketch.1. |
If you want to select another support for the cutout,
click on and select your
new support. It can be a web, a flange or the planar part of the
surfacic flange. |
|
|
 |
Specifying the support for
the cutout avoid confusions in case of overlaps. |
|
In the following example two flanges are overlapping
each other. |
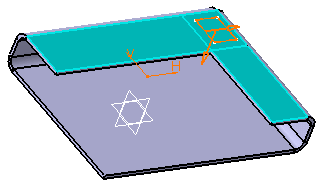 |
If you
try to create a cutout on such a part, the following message is
displayed: |
|
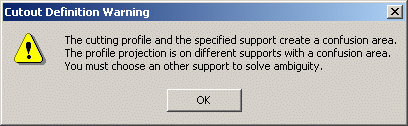 |
|
To avoid this,
you have to select the exact support for the cutout. |
|
|
|
 |
|
|
|
-
Click Cutout
.The
Cutout Definition dialog box is displayed
-
Select Sheetmetal pocket
as Cutout type in the combo box.
The skin to be impacted remains grey and the End limit type is disabled.
-
Set the Depth to 1mm.
-
Select Sketch.1 as profile.
A preview of the cutout is displayed. In our example, the cutout
will impact only half the base feature. |
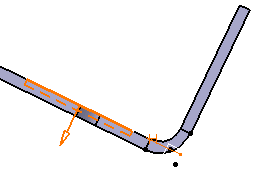 |
-
Click OK
in the Cutout Definition
dialog box.
The cutout is created. |
|
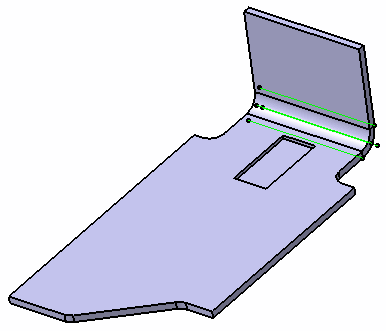 |
-
In the specification tree, double click on Cut Out.1 to
display the Cutout Definition dialog box.
-
Click More>> to display the maximum
information.
The Direction is already selected (Sketch.1). By default, it is
set as normal to the profile. |
|
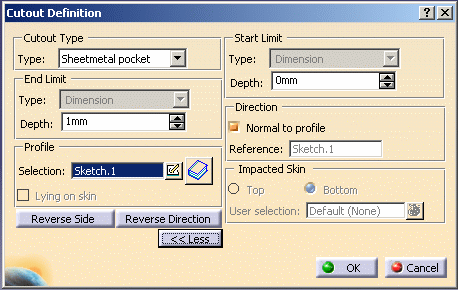 |
-
Uncheck
Normal to profile.
-
Click inside the
Reference
field to activate it.
-
Select Line.1 to perform a cutout normal to the line
direction.
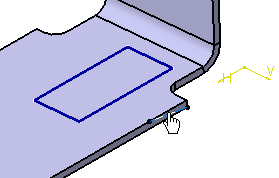 |
|
 |
Should you need to create a line, right-click on the
Reference
field and select
Create Line. |
|
 |
|
Refer to
Creating
Lines for further information. |
-
Click OK to create a cutout normal to the line
direction.
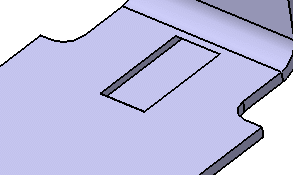 |
|
 |
- The pocket cutout can be created only on a planar and
monosupport surface (i.e. a web a flange or the planar face of a
surfacic flange).
- May you want to create a cutout on an overlapping element or a
bend with radius=0, either choose the top skin of the element (as
shown in the picture above), or unfold the part to create the
cutout.
- You cannot create a pocket cutout on a stamp or a surfacic
flange.
- You cannot create
- a standard cutout on a pocket cutout
- a standard cutout on a feature impacting a pocket cutout.
- You can create
- a pocket cutout on a standard cutout.
- a pocket cutout on a pocket cutout,
|
|
|
 |
Once the Reference Direction and the Objects
Support fields are filled in, the selection can be modified but
cannot be cleared. |
|
Cutouts can be created directly on the
unfolded view of the part. |
|
You can click Catalog
to
open the
Catalog Browser. |
|
|
 |
- Refer to Component Catalog Editor
documentation to have further information on how to use catalogs.
- Refer to the Create a Pocket task in the Part Design User's
Guide for further details on how to create cutouts.
|
|